Our Services
Process evaluation
We analyze your assembly process and identify the disruptive factors together. You will receive clear solutions, allowing you to focus on a secure process.
Workshop
Together with your team, we identify the damage potential in your components & systems and structure logical steps to achieve your goals.
Training
Through comprehensible and practical training measures, we prepare your team for the requirements, risks, and behaviors surrounding technical cleanliness according to VDA19.1 & VDA19.2 recommendations.
Component analysis
Through valid and non-destructive sampling using air or extraction fluids, you receive a precise evaluation of the particle load on your components & systems.
Risk assessment
We analyze your component for potential damage effects and identify the weaknesses. This allows you to adapt your processes or design accordingly.
Standard creation
We work with you to develop limits for your component and demonstrate their attainability through analyses. You will receive a specific specification for your component for your plant or suppliers.
After-sales
Your GLÄSER test machine is in the best hands with us. Your machine will be maintained on-site and supplied with original spare parts, ensuring the long-term functionality of your test machine.
Process evaluations / consultations
The challenges of achieving required limits and maintaining the desired cleanliness levels have many facets.
- Are you faced with the task of optimizing your assembly processes to meet required cleanliness specifications?
- Would you like a reliable and practical assessment of your processes regarding the current particle load level in your production?
- Do you need a structured and realistic action list that enables you and your team to sustainably reduce the particle load?
- If you can answer any of these questions with “yes,” then let’s discuss your project and challenges.
- Feel free to contact us informally, and we will arrange a meeting with you for an initial non-binding exchange.
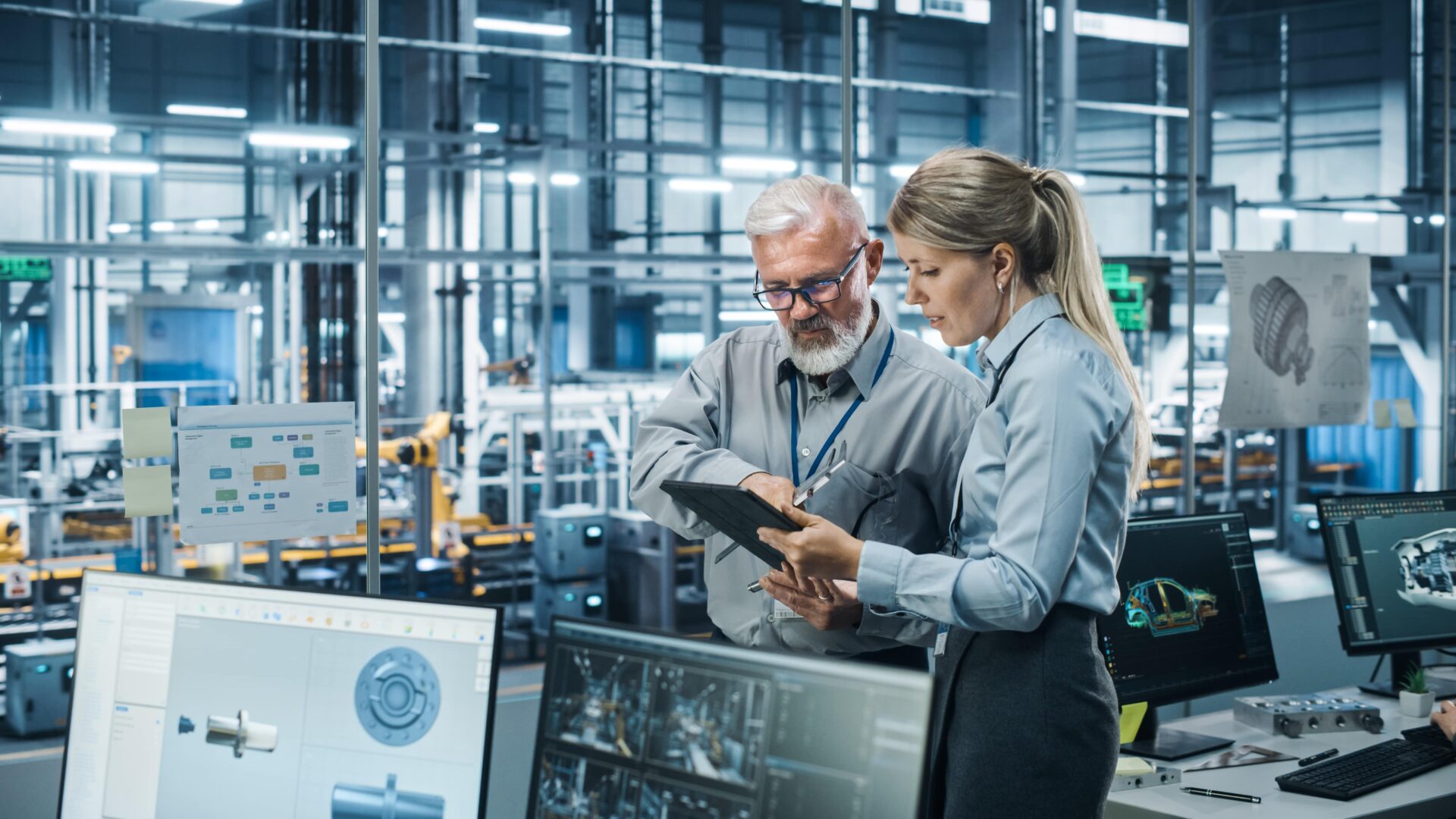
Preparation
Before any consultation, process evaluation, or assessment, thorough preparation is necessary.
We work on this together with you – closely and trustingly.
- You share your specific challenges with us and define your desired goal.
- You provide us with the necessary documents for preparation. You will receive a checklist in advance.
- Using particle extraction, we determine the current cleanliness level of your components.
- After assessing the current state, we evaluate your challenges and agree on the next steps with you.
- Due to many years of experience, our experts will find the right solution.
- You receive a specific offer and a description of our service scope.
- We arrange an on-site appointment for the consultation.
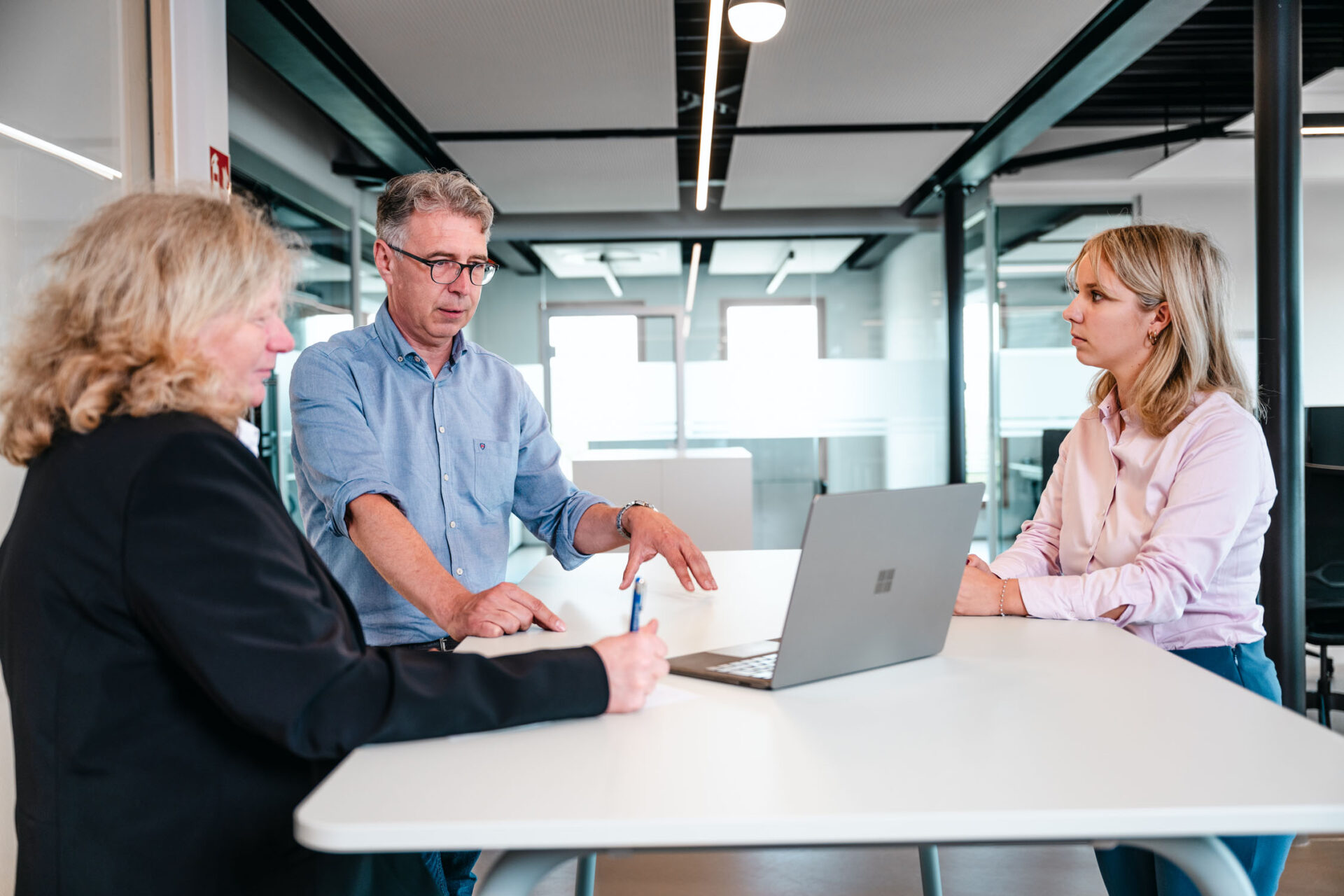
Execution
In the execution of process evaluations & consultations, we follow a comprehensible approach, examining not only the assembly itself but also upstream and downstream processes.
This is the only way to provide a meaningful and complete evaluation of the process.
- With your team, we first address the conditions for applying and documenting methods to determine particle contamination on functionally relevant components according to VDA19.1/ISO16232 recommendations.
- To determine particle load under assembly conditions, we use practical equipment at critical stations.
- Using a logically structured questionnaire, we work with you point by point to identify the disruptions in the plant.
- We discuss the concepts for cleanliness in assembly with you and identify possible sources of errors.
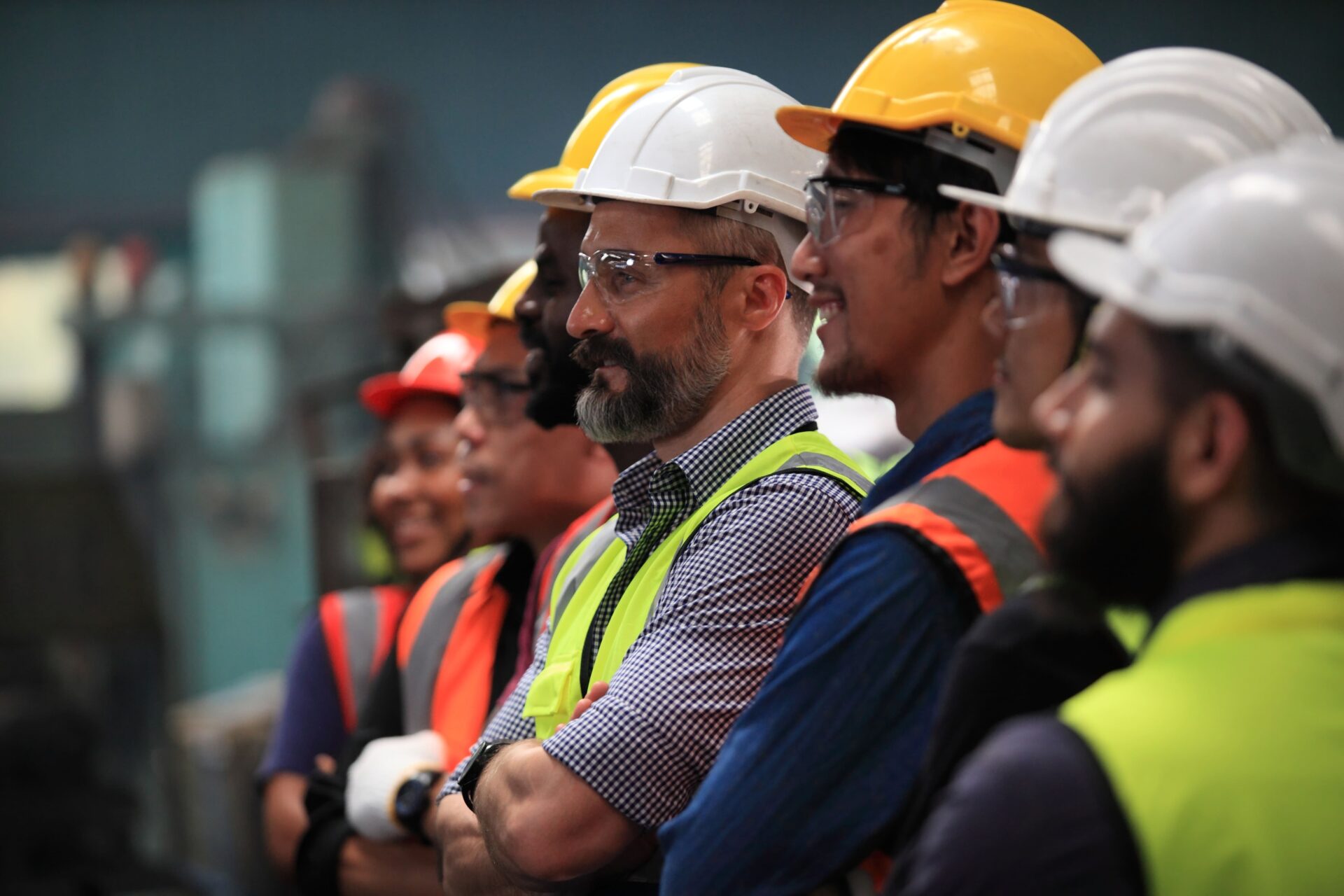
Result
The quality of a process evaluation is evident in the elaboration of the results:
A clearly understandable and realistic documentation of identified potentials and a practical list of measures to improve technical cleanliness for your specific requirements.
Upon completion, you will receive a detailed and comprehensive report on the identified deficiencies concerning particle loads.
The report includes:
- Analysis results of environmental measurements at assembly stations & areas
- Elaboration of weaknesses in your production and environment in text and images
- Clearly understandable and actionable recommendations for each individual topic
- Action list with an assessment of the required implementation effort
- Achievement level (target vs. actual) for each area
- Concept proposal with concrete implementation steps
We will discuss this with you.
This will enable you to adjust your processes to best ensure the requirements for technical cleanliness.
The result of a consultation is the starting signal for a secure quality process.
We are happy to continue accompanying you on your way to a clean production.
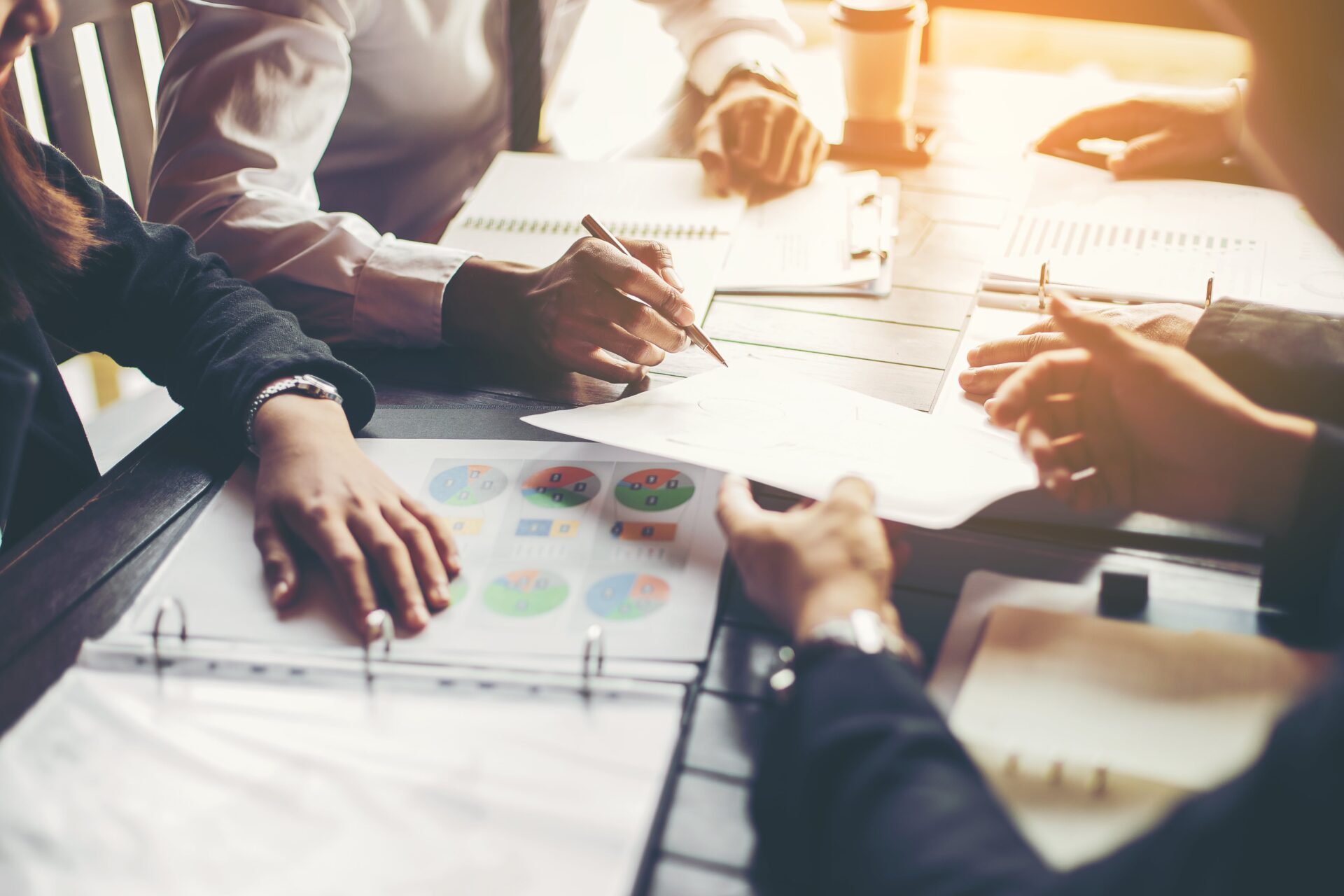
Our Workshops
Together towards success
The design of the component, the choice of suppliers and materials, the production and ultimately your customer have a lot in common:
- Defining and adhering to cleanliness requirements for a component.
- In a workshop, we work with you to develop specific goals.
- Each employee has valuable and specific knowledge in certain areas.
- Often, this knowledge is not or insufficiently available in other areas.
- Through a workshop, we work together to identify and prioritize potentials.
- You will receive a comprehensive report detailing the most important aspects of the workshop.
The report forms the basis for further action.
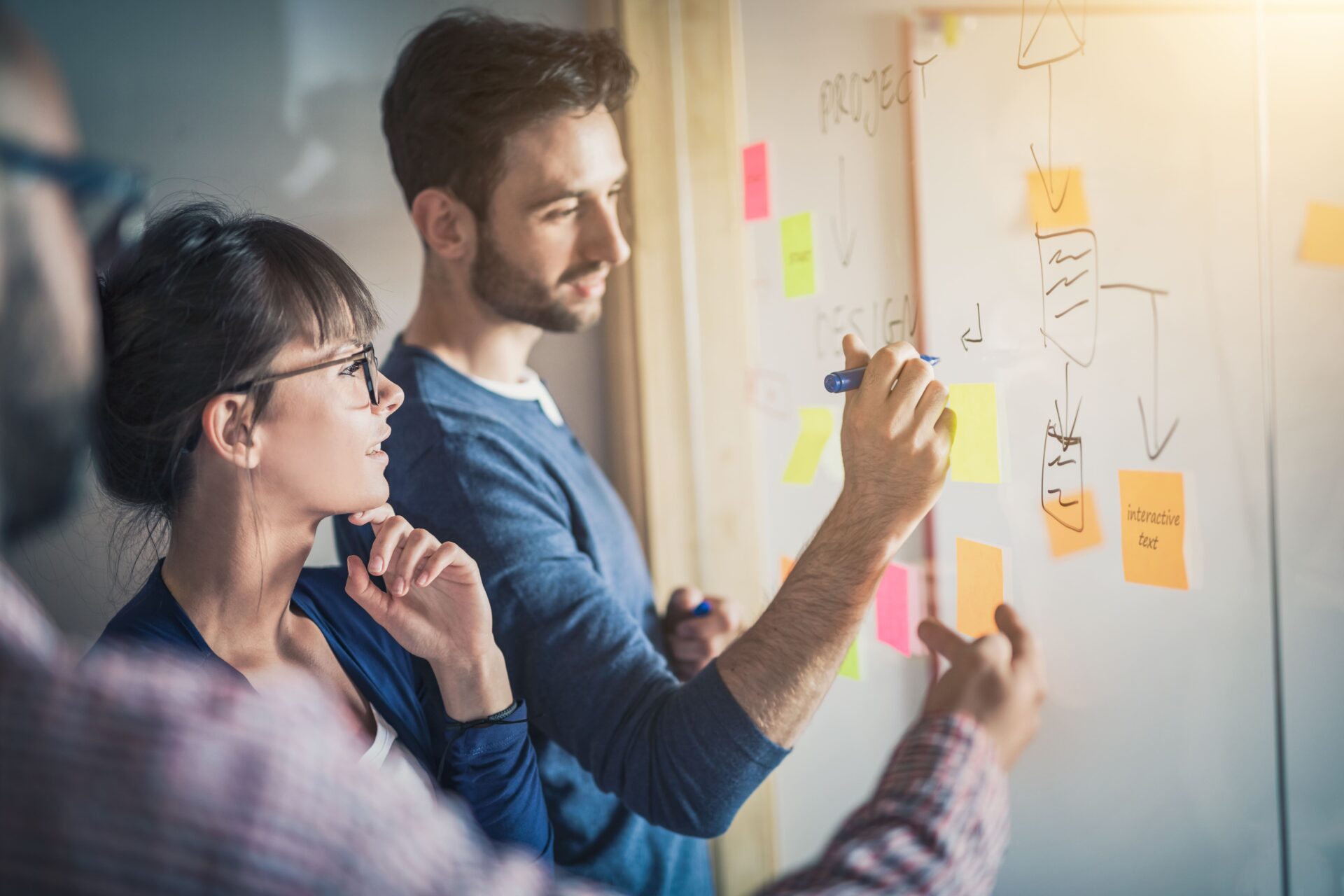
Component analyses
We know your particles
To meet the required limits from cleanliness specifications, it is essential to perform this through particle extraction from the component using appropriate test machines.
- There is an optimal extraction method available for each of your applications.
- Before the actual sampling, the extraction parameters are validated using a decay curve.
- We document the particle load according to VDA19.1 / ISO16232 recommendations in a meaningful and clear report.
- In addition, we offer you an intuitive tool in the form of our CleanTec laboratory database. Analysis results and other data can be filtered and are clearly displayed.
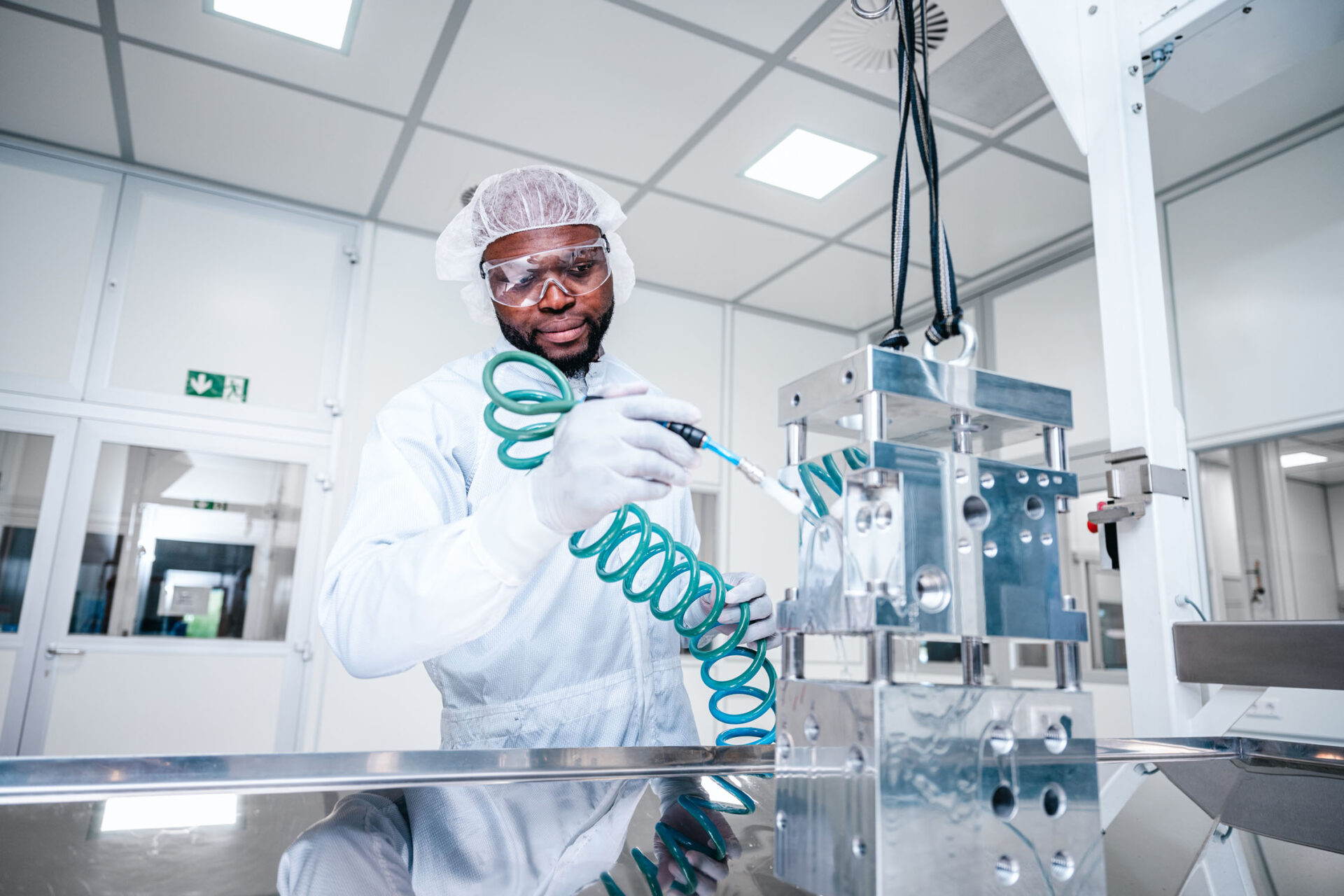
Creation of Standards
We create your own standard specification
New technologies require new manufacturing processes.
There is no shortage of existing standards & specifications for technical cleanliness.
Nevertheless, it is increasingly necessary to create specifications for new components or component groups.
For example, existing standards & specifications are no longer sufficient for fuel cells, electrolysis stacks, battery cells, high-voltage connectors, or sensors.
We support you in developing a specification tailored to your product, incorporating all necessary standards and references.
We define:
- Cleanliness classes and limits for your component
- Extraction and analysis methods
- Recommendations for assembly cleanliness for your production or suppliers
With our many years of experience and over 100,000 component analyses conducted, we have access to more than 700 specifications from the following industries:
- Automotive industry
- Aerospace
- Medical technology
- Electronics industry
- and more…
Benefit from our know-how and create your own specification with us to ensure the functionality of your component or system.
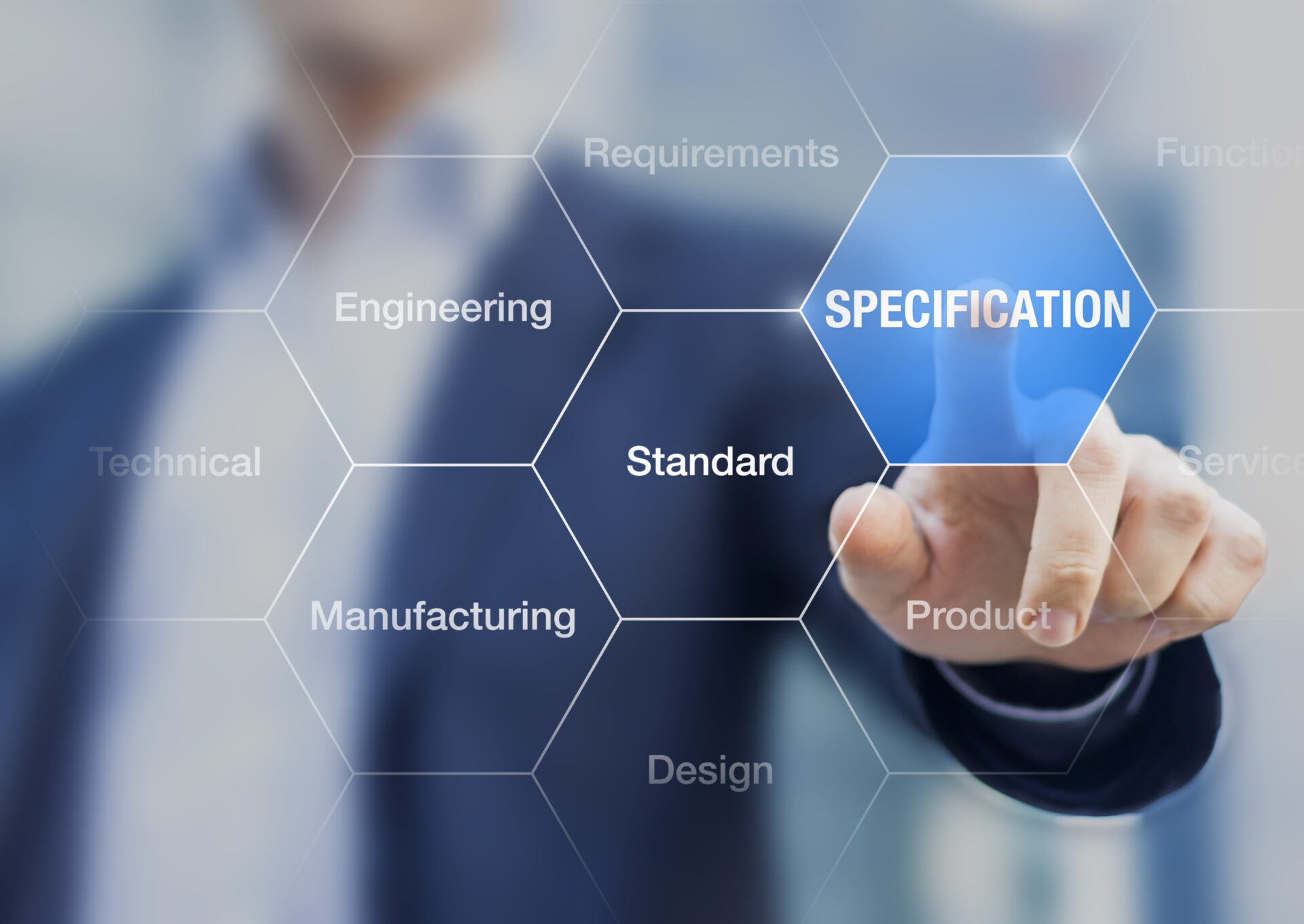
Risk assessment
Identify the weaknesses of your component with us
To evaluate weaknesses in your component, we recommend conducting a risk assessment.
This requires a thorough understanding of your component and its function.
In a meeting on-site or in our laboratory, the weaknesses of the component are identified.
The probability of malfunction or failure of individual components is recorded and documented.
Regardless of whether it is:
- Short-circuit probability on circuit boards
- Possible clogging of capillaries in a bipolar plate
- Generation of particles due to materials used
We find the deficiencies and present them validly and comprehensibly.
This enables you to optimize the design or processes around your component.
Thus, the best possible safety for your product is ensured.
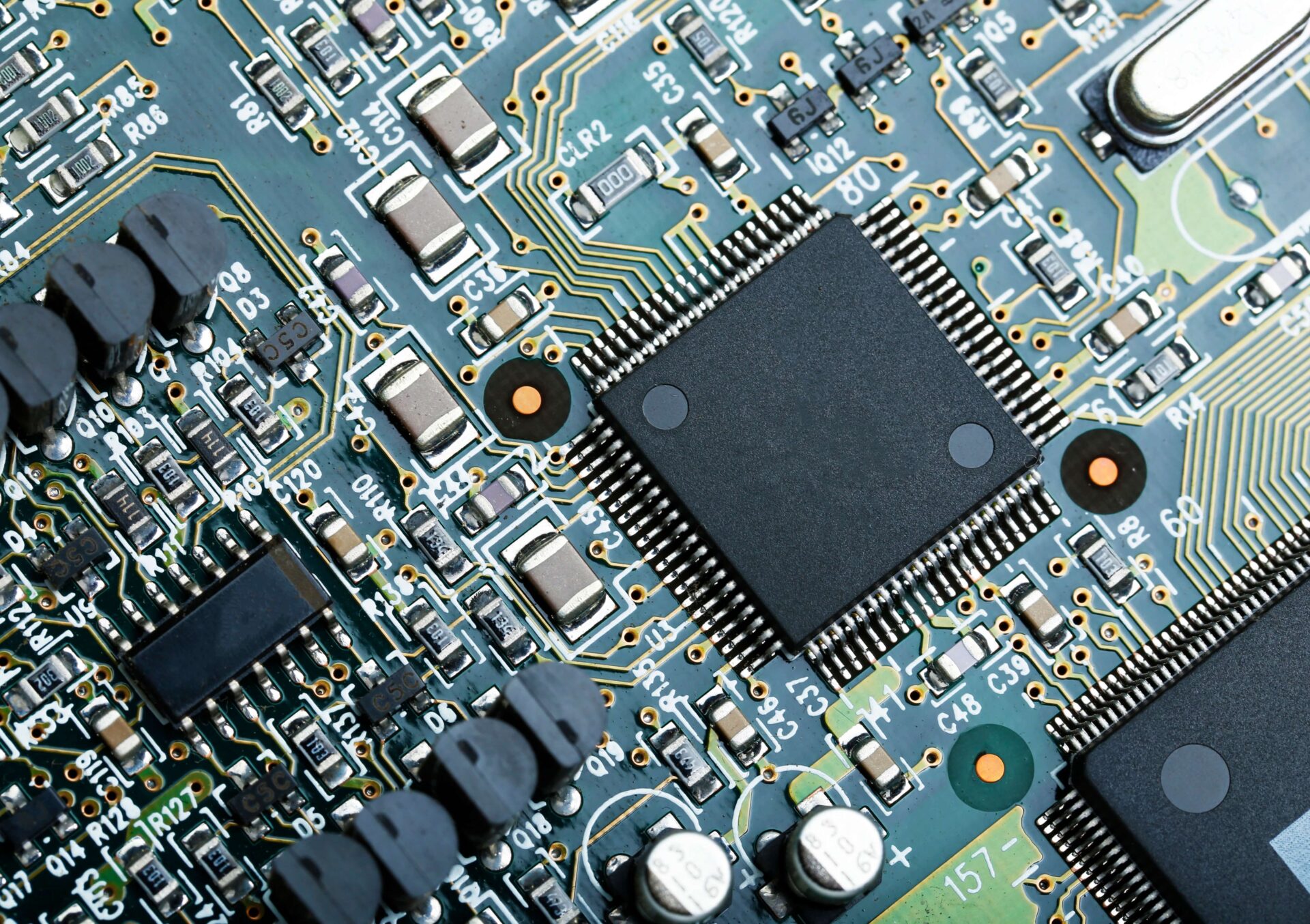
Training / workshops
Qualify your employees in technical cleanliness
Prepare for technical cleanliness and qualify your employees for responsible handling of the challenges in your process chain.
This way, unnecessary sources of error and associated costs are avoided from the outset.
As a leading accredited laboratory, we offer you a wide range of training programs:
According to your requirements, on-site or comfortably at Gläser.
With the speakers of the Gläser team, you have experienced experts at your side.
They have extensive experience and practice as active members of standardization committees as well as through the experience of thousands of laboratory examinations.
Take a look at our current training program and contact us.
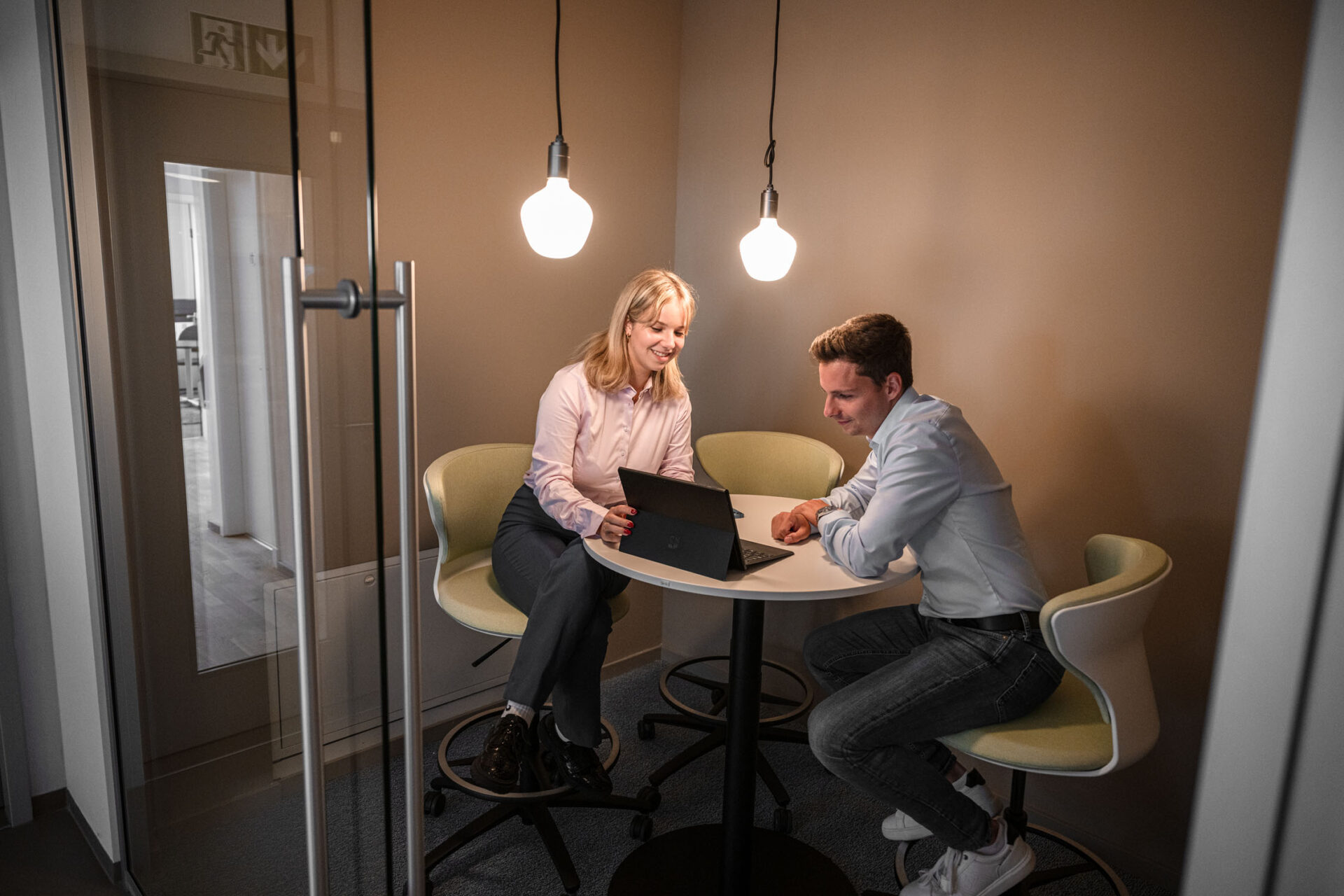
Webinar
Online basic training
Expand your knowledge quickly and easily
Obtaining basic knowledge on technical cleanliness regarding particulate contamination has never been easier than with our compact online webinar.
Gain an overview of:
- Basic rules of technical cleanliness
- Sources of particles
- Damage mechanisms
- Terms / regulations
- Extraction methods and procedures
- Basics of assembly cleanliness
Simply register for the online webinar for free using the following LINK and learn everything you need to know about technical cleanliness.
After the webinar, one of our experts will be personally available for further or emerging questions.
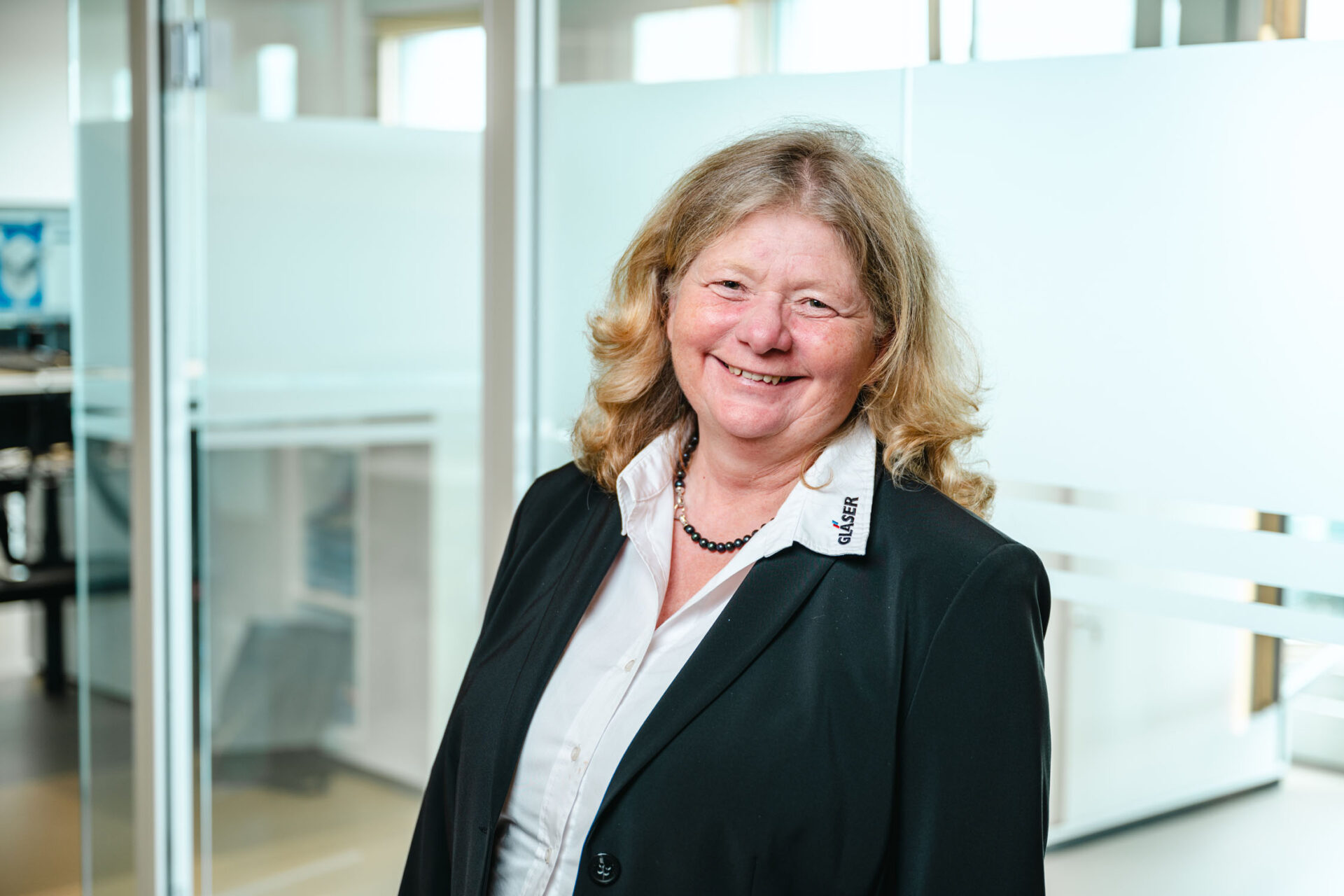
Seminars for technical cleanliness
Discover the world of technical cleanliness with our open seminars
Our open seminars offer you the unique opportunity to specialize in a diverse field that is critical to many industries. Learn how to master the strict specifications and limits required in the production of components for the automotive industry, the manufacture of electrolysis stacks, fuel cells or battery cells. Our experts will guide you through the world of particle extraction and analysis to identify contamination and take effective action.
With practical best-practice examples, we show you how to understand and manage contamination in the best possible way. Our seminars are the key to acquiring the necessary knowledge and correctly interpreting the correlations.
Take the opportunity to learn and grow with our seminars!
Simply register at experts@glaeser-group.com and find out everything you need to know about technical cleanliness.
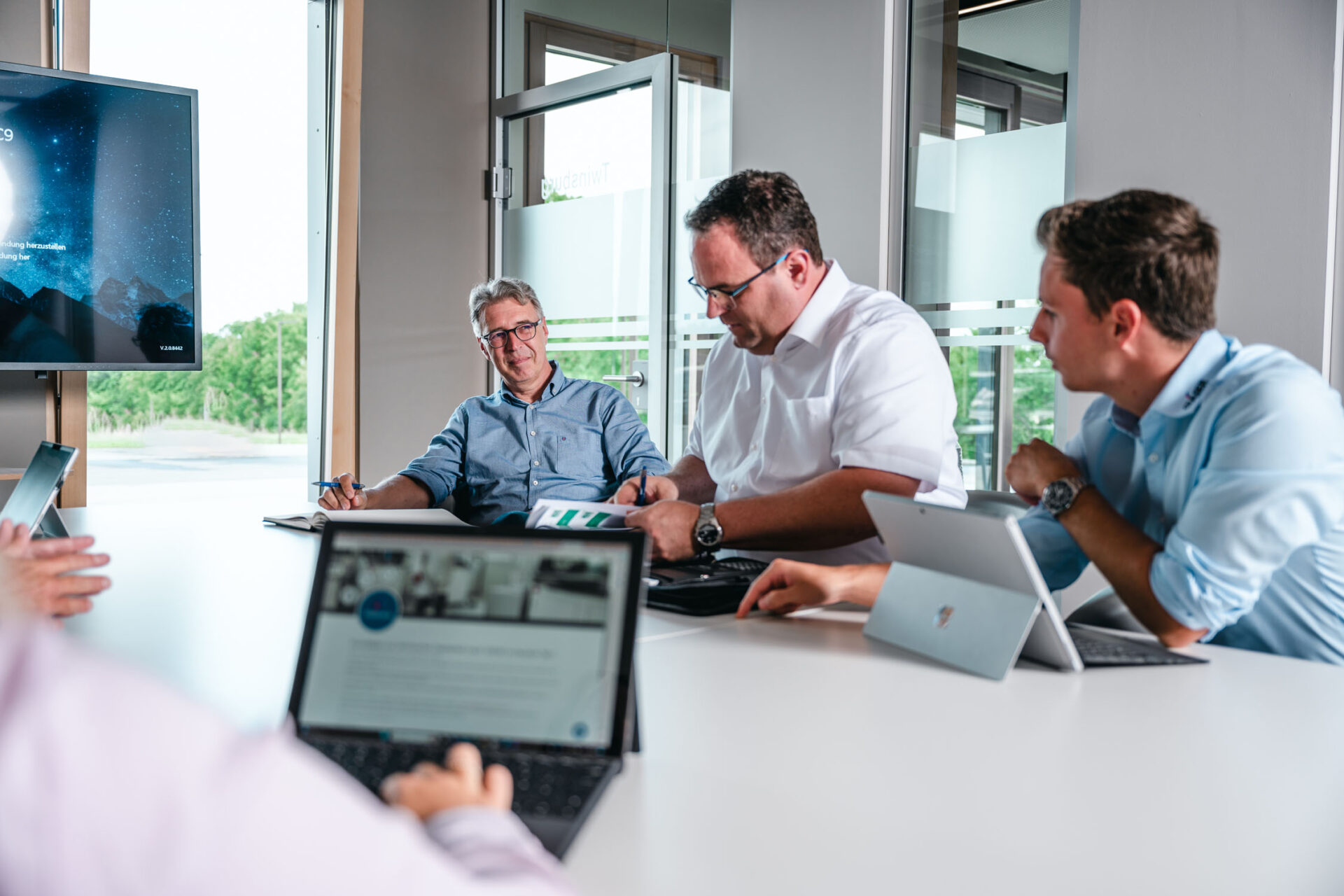
After-Sales
Our service does not end with the sale
A GLÄSER test machine is easy to use, durable, and robust.
To keep it that way, we offer you a variety of services that ensure the quality & function of the GLÄSER test machine in the long term.
Preventive maintenance maximizes the lifespan of your test machine.
Professional inspection and cleaning by one of our service technicians maintain the functions and basic cleanliness.
The achievement of safe blank values as well as the precise functioning of your machine is guaranteed.
Additionally, we check:
- Sensors
- Electrical components
- Hydraulics
- Safety
- Functionality
In this way, your extraction cabinet is well-prepared for continued operation.
As part of a maintenance contract, we take over the control effort and inform you in good time about maintenance intervals.
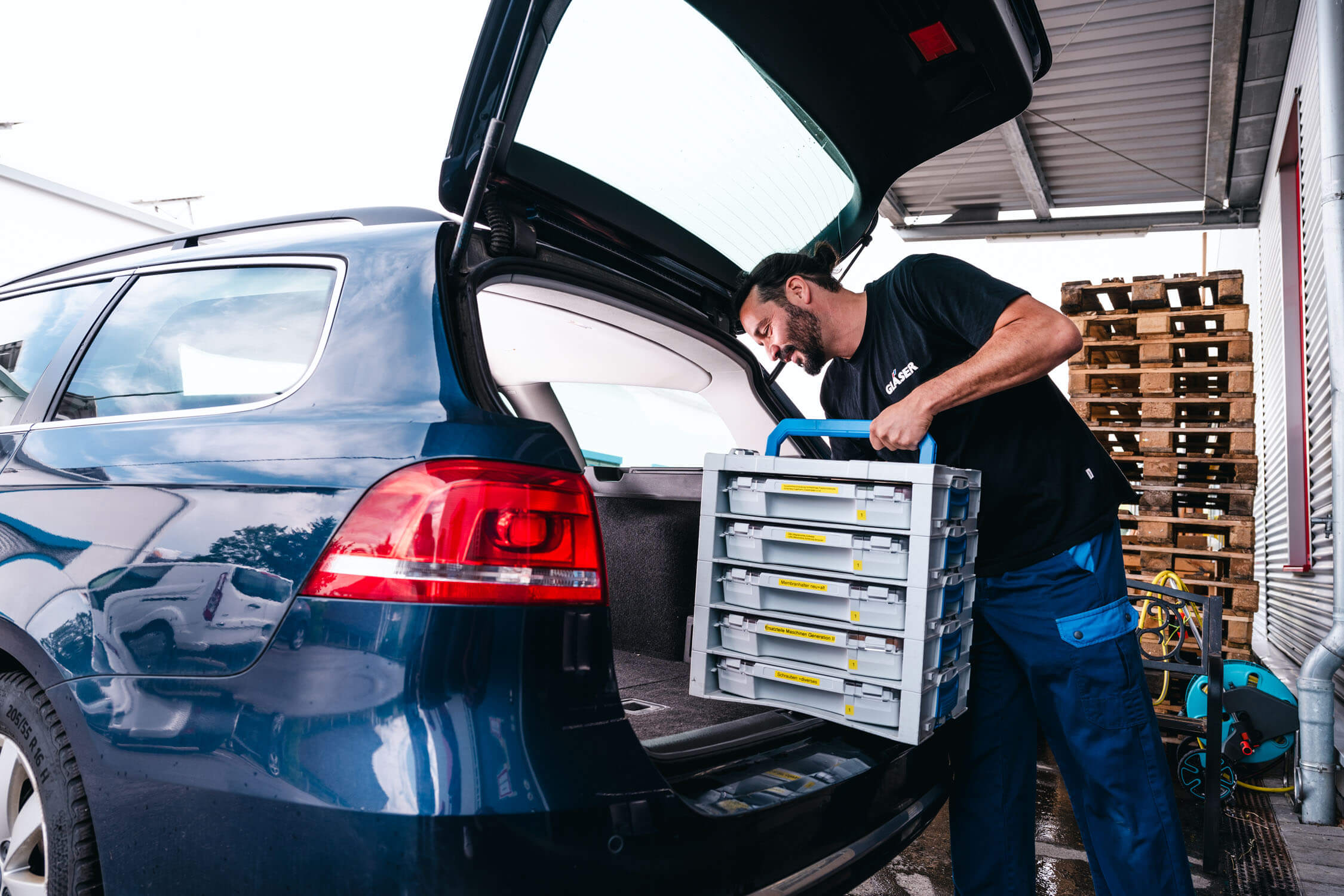
Maintenance contracts
Sign an annual maintenance contract with us.
You take care of almost nothing; we handle it.
Our expert team contacts you in good time and arranges a maintenance appointment.
BENEFITS
- Permanently low maintenance price
- Optimally maintained test machine
- Extension of warranty
- Reduced probability of failure
- Planning reliability
- Professional advice
- Comprehensive maintenance report
Original spare parts
Should the unlikely event of a malfunction occur, contact us.
We identify the problem and deliver the correct spare part.
BENEFITS
- Quality assurance
- Perfect fit
- Durability
- Warranty claims
- Safety
- Maintenance friendliness
- Value retention
- Efficiency
- Compatibility
- Availability