Partikelanalysen im akkreditierten Prüflabor
Erhöhen Sie Ihre Produktqualität durch die Optimierung von Produktionsprozessen mithilfe der Technischen Sauberkeit. Gläser CleanTec ist hierfür Ihr kompetenter Ansprechpartner.
Mit modernster Laborausstattung untersucht unser bestens ausgebildetes Laborteam Ihre Bauteile auf partikuläre und chemisch-filmische Verunreinigungen im hauseigenen und nach ISO 17025 akkreditierten Labor mit einem Reinraum nach ISO 14644 der Klasse 7. Ob groß oder klein, wir können auf Ihre individuellen Anforderungen eingehen und führen Partikelextraktionen an Kleinstbauteilen im mg-Bereich bis hin zu Großbauteilen mit bis zu 350 kg Gesamtgewicht durch.
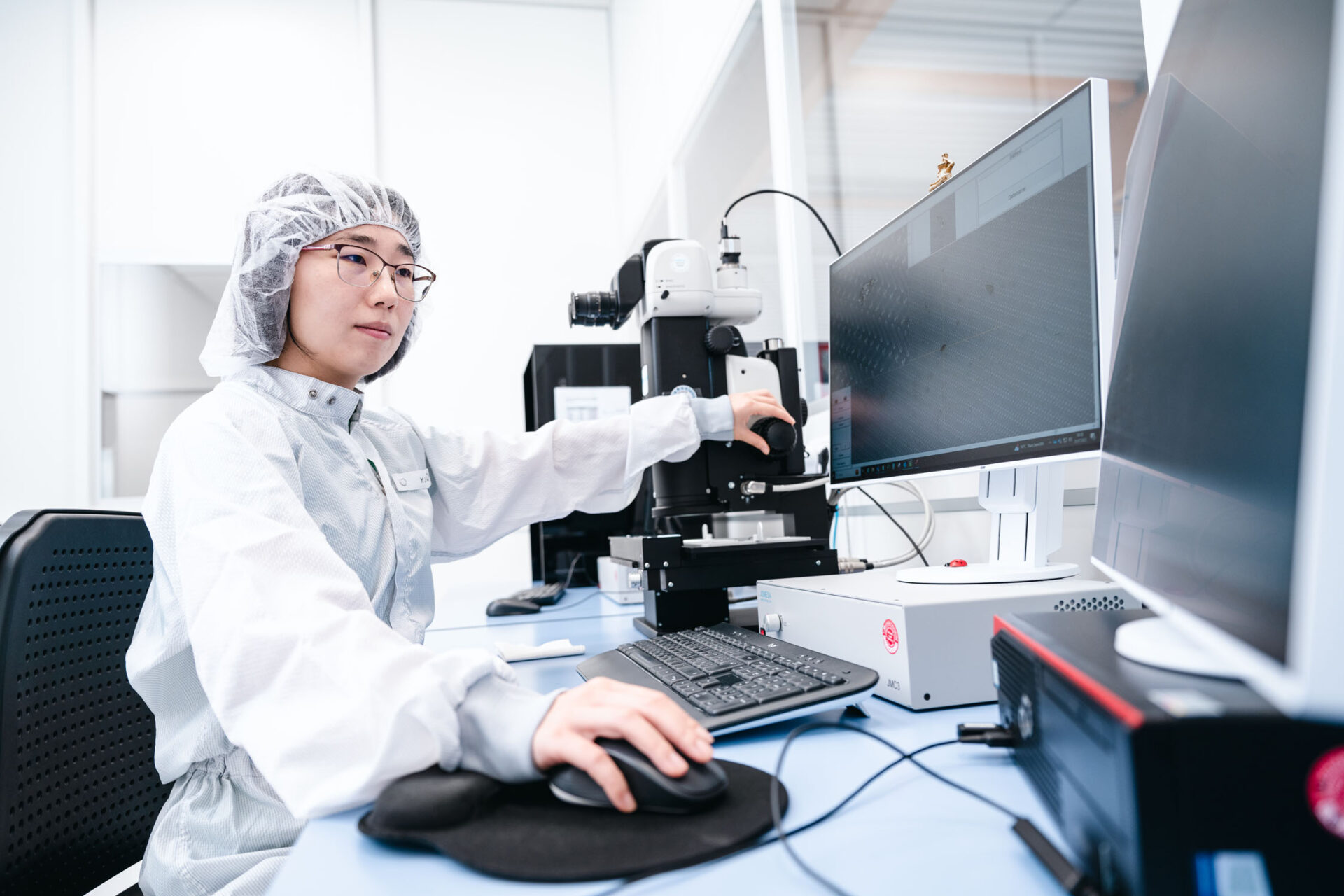
Unsere Dienstleistungen
Sauberkeitsanalysen/ Restschmutzanalysen
Bestimmung der partikulären Verunreinigung Ihrer Bauteile
Materialanalysen Ihrer Partikel
Weiterführende Analysen zur Bestimmung der Partikelherkunft und Schädigungspotentials
Chemisch-Filmische Analysen
Bestimmung von organischen, ionischen und chemischen Verunreinigungen auf Bauteilen
Flüssigkeit/ Öl-Analysen
Bestimmung der partikulären Verunreinigung in Flüssigkeiten oder Ölen nach ISO 4406/ISO 4407
Partikelmonitoring
Bestimmung der Partikelfracht in der Umgebung und auf Oberflächen
Q&A
Eine technische Sauberkeitsprüfung bezieht sich auf den Prozess einer Überprüfung und Bewertung, beispielsweise eines Bauteils hinsichtlich ihrer Sauberkeit.
Das Ergebnis einer solchen Prüfung liefert Angaben auf die verbliebene Art, Menge und Größe der Schmutzpartikel nach Entnahme des Bauteils (meist nach dem Endreinigungsprozess).
Die technische Sauberkeitsprüfung umfasst typischerweise verschiedene Schritte:
– Analyse der Anforderungen (Spezifikationen nach denen das Bauteil geprüft werden soll)
– Probennahme meist nach dem Reinigungsprozess, also in dem Zustand in welchem das Bauteil weiter verbaut werden soll
– Extraktion der Partikel des Bauteils, also das Ablösen der Partikel des Bauteils und Auffangen der Partikel mittels eines Analysefilters
– Analyse des Analysefilters mittels Lichtmikroskop, um die Partikel zu vermessen, zu zählen und in metallisch glänzend, nichtmetallisch glänzend und Fasern zu unterscheiden
– Bewertung der Ergebnisse im Vergleich zu festgelegten Sauberkeitsstandrads / Spezifikationen
– Dokumentation der Ergebnisse und ggf. Implementierung von Maßnahmen zur Verbesserung der Sauberkeit
Die Anzahl der Bauteile, die für eine Standard-Sauberkeitsprüfung zu verwenden sind, ist in der VDA19.1 / ISO16232 klar geregelt.
Zunächst ist herauszufinden, welche Oberflächen / partielle Bereiche des Bauteils geprüft werden müssen (cm²)
Dazu ist es bei der Prüfung u.U. nötig, Teilbereiche zu maskieren
Ist das gesamte Bauteil zu Prüfen dann gilt:
– Es sind so viele Bauteile einer gleichzeitigen Prüfung zu unterziehen die eine Gesamtoberfläche von 200cm² aufweisen.
– Somit wären bei einem Bauteil von 20cm² Oberfläche, insgesamt 10 Bauteile für diese Prüfung zu Verfügung zu stellen.
– Darüber hinaus ist auch zu klären, ob bereits eine Abklingmessung dieses Bauteils erstellt wurde, ansonsten vervielfacht sich die Menge der Bauteile schnell.
Die Wirkung des Extraktionsverfahrens entscheidet darüber, ob die Sauberkeit des Bauteils richtig beurteilt werden kann.
Deshalb ist bei einer Sauberkeitsprüfung nachzuweisen, dass lösbare Schmutzpartikel möglichst vollständig vom Prüfbauteil extrahiert werden.
Da es keine absolute Bestimmungsmöglichkeit der tatsächlich vorhandenen Partikelfracht gibt, werden Abklingmessungen durchgeführt.
Durch wiederholte Beprobung des Bauteils wird festgestellt, ob die jeweils abgelöste Partikelfracht abnimmt und somit ein geeignetes Extraktionsverfahren vorliegt.
Dass die zu analysierenden Verunreinigungen hinreichend vollständig abgelöst sind, wird über das sog. Abklingkriterium bestimmt.
Darüber wird der Punkt der Abklingkurve bestimmt, an dem der letzte extrahierte Schmutzwert kleiner als 10% der bisher extrahierten Gesamtschmutzmenge ist.
Dieser Punkt wird zur Ausarbeitung der Routineprüfprozedur verwendet.
Prozedur:
-Festlegung einer voraussichtlich geeigneten Prüflosgröße
– Prüfeinrichtungen aufreinigen und Blindwertmessung durchführen
– Extraktionsprozedur mit Startparametern 6x hintereinander anwenden
– Nach jedem Extraktionsschritt, Prüfeinrichtung nachspülen
– Berechnung des Verhältnisses zwischen Sauberkeitswert und der Summe aller durchgeführten Extraktionsschritte
– Bei Erreichen des Abklingkriteriums, Ausarbeitung der Routinebeprobung
– Bei Nichterreichen, Extraktionsparameter anpassen und mit einem neuen Bauteil wiederholen
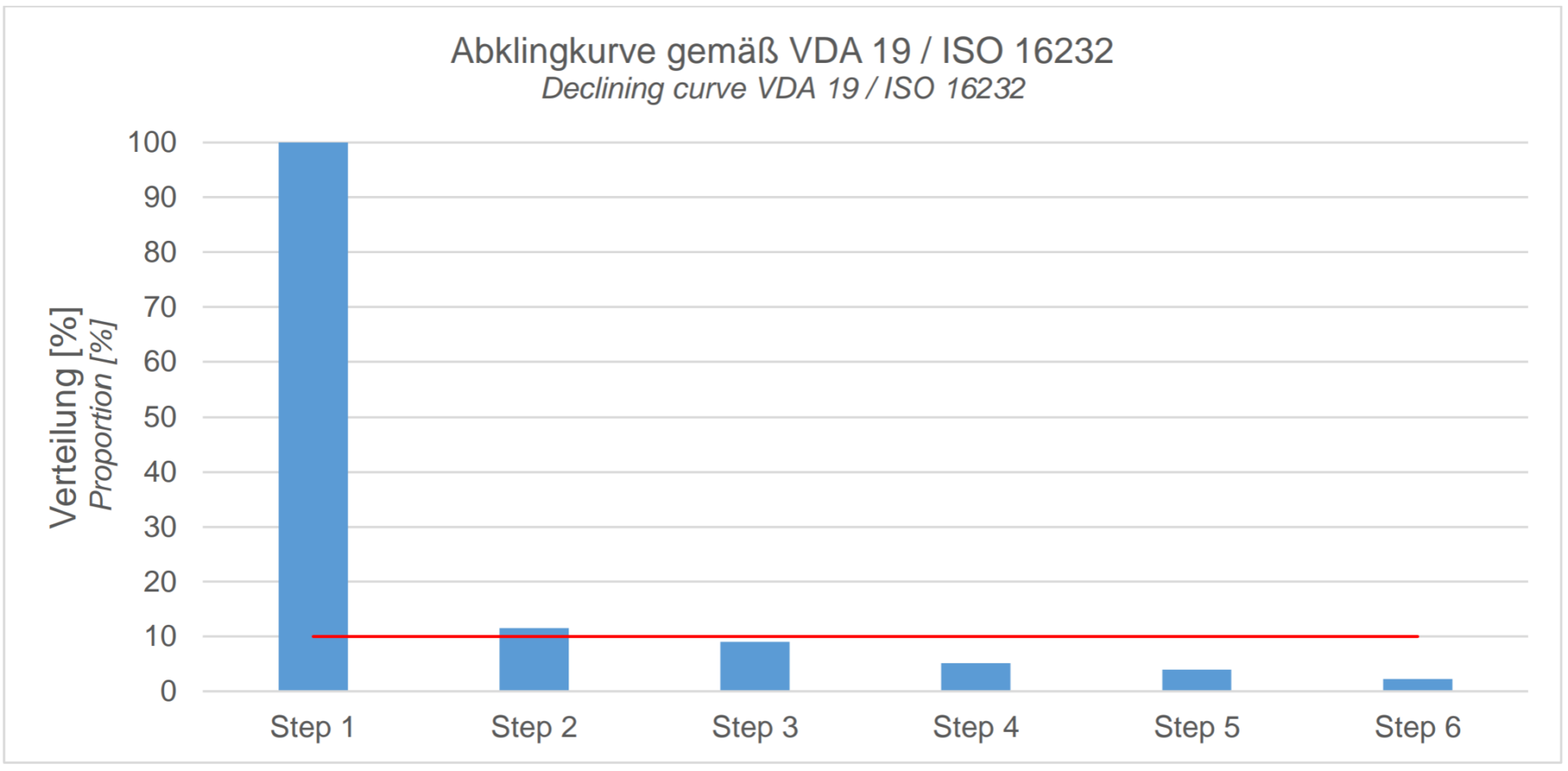
Die Zweifachprüfung wird angewendet, wenn:
– die Extraktionsparamater auf ihre Wirksamkeit geprüft werden sollen
– die Abklingmessung und dadurch ermittelten Paramater durch eine Zweifachprüfung bestätigt werden sollen
– das Bauteil von einem anderen Bauteil nur minimal abweicht und die durchgeführte Abklingmessung und deren Ergebnisse vom ersten Bauteil geprüft werden sollen
Bei der Zweifachprüfung wird das Bauteil, anders als bei der Abklingmessung, zwei Mal an einem noch nicht beprobten Prüflos durchgeführt und die Sauberkeitswerte ermittelt.
Ist der zweite Sauberkeitswert kleiner/gleich 30% der Summe der beiden Sauberkeitswerte, sind die ausgearbeiteten Routinebeprobungsbedingungen geeignet.
Diese können als Prüfspezifikation festgeschrieben werden.
Somit spart eine Zweifachprüfung u.U. Zeit und Geld, dient in den meisten Fällen aber als zusätzliche Absicherung der festgelegten Routinebeprobungsparameter.
Vor jeder Standardbeprobung, einer Qualifizierungsuntersuchung oder einer Zweifachprüfung muss nachgewiesen werden, dass nur Partikel vom Prüfbauteil in das Analyseergebnis eingehen.
D.h. der Blindwert wird VOR der eigentlichen Extraktion eines Prüfbauteils durchgeführt und erbringt den Nachweis, dass alle nicht vom Bauteil stammenden Partikel (Fremdpartikel) so gut wie möglich ausgeschlossen werden und nicht zu falschen Interpretationen bei der Beurteilung des Sauberkeitszustands des Prüfbauteils führen.
Ursache für Fremdpartikel können sein:
– Prüfflüssigkeit und Nachspülflüssigkeiten
– Extraktionsgerätschaften (Wannen, Becken, Leitungen, Ventile,..)
– Handhabung während der Beprobung und Analyse
– Umgebung und Personal
– Sämtliche Gegenstände, die in Kontakt mit dem Bauteil und der Prüfflüssigkeit kommen
Der zulässige Blindwert wird ausgehend von den Sauberkeitswerten des Bauteils rechnerisch ermittelt und darf 10% des geforderten/voraussichtlichen Sauberkeitswerts des Bauteils nicht überschreiten.
Um dies möglichst effizient zu erreichen, ist die Auswahl des richtigen Extraktions-Equipments von entscheidender Bedeutung.
Das Thema ist hiermit nicht abschließend erläutert, bietet aber einen grundsätzlichen Überblick über die Begriffsdefinition.
Die Überschreitung der geforderten Partikelgrenzwerte hat viele, nahezu unzählige Gründe:- Umgebungssituation / Räumlichkeiten- Lüftungstechnik / Klimaanlagen / Heizungen / Lüftungsanlagen- Arbeitskleidung- Reinigungskonzepte bzw. Schwachstellen darin- Handhabung durch nicht ausreichend geschultes Personal- Waschprozesse vor Verpacken der Bauteile- Verpackung selbst- Logisitk- …Oft ist es eine Kombination aus mehreren dieser Faktoren, die zu einer Verfehlung der Grenzwerte führen.In solchen Fällen ist zunächst mittels wiederholender Prüfungen sicher zu stellen, ob diese Überschreitung auch bei weiteren Bauteilen eintritt.Ist dies der Fall, kann ein externes Dienstleistungslabor zu Rate gezogen werden, welches die gleiche Beprobung durchführt und die Ergebnisse dann mit Ihren verglichen werden können.Bleibt es dabei und die Grenzwerte werden weiterhin überschritten, dann können Sie Folgendes tun:- Sie beauftragen einen externen Dienstleister damit, Ihre Fertigung nach Empfehlungen der VDA19.1/ISO16232 & VDA19.2 zu evaluieren- In einem Workshop wird zunächst einmal mit Ihrem Team erarbeitet, welche Einflussfaktoren möglich sind und wie die Situation bei Ihnen eingeschätzt wird- Anschließend wird die Umgebungssituation mit Hilfe von Partikelfallen (Monitoring) und einer Inspektion des Werks vom Wareneingang bis zum Warenausgang durch Experten der Technischen Sauberkeit bewertet- Durch Interviews mit Monteuren Ihrer Produktion, Fotos von festgestellten Schwachstellen und die Bearbeitung eines umfangreichen Auditkatalogs erhalten Sie nicht nur konkrete Informationen über die Schwachstellen in Ihrer Fertigung, sondern mittels ausführlichen und klar strukturierten Reports eine Actionlist und Empfehlungen zur Beseitigung der Schwachstellen- Im weiteren Verlauf ist es sinnvoll, sich auf dem Weg zur Erreichung der Grenzwerte weiterhin begleiten zu lassenErfahrungsgemäß ist eine solche Begleitung nicht nur hilfreich, sondern nötig.Der Umfang einer externen Beratung richtet sich nach der Komplexität der Aufgabe.Manchmal ist es mit wenigen Online-Terminen bereits getan, in manchen Fällen ist es aber notwendig, sich gründlich und vor Ort Zeit zu nehmen, um die Herausforderungen konkret und dauerhaft bestmöglich zu beherrschen.
Sie regelt nicht ausdrücklich einzelne Partikeltypen (Fasern, metallisch glänzend,) und auch die Partikelbreite wird damit nicht geregelt.
Bei der Codierung wird die Partikelanzahl einer Konzentrationsklasse (engl.: contamination level) zugeordnet.
Bsp.: CCC = A(B20/C16/D12/E10/F10/G9/H6/I3/J2/K1/L0/M0/N00)) (Drei Bezugsgrößen: A= pro 1000cm², V= pro 100cm³ und N= pro Bauteil)
Bei A und V werden die Partikelanzahlen codiert angegeben, bei N nicht.
Um diesen Code nun eindeutig zu entschlüsseln, werden nachstehende Tabellen benötigt. Diese finden Sie in der VDA19.1 Kapitel 9
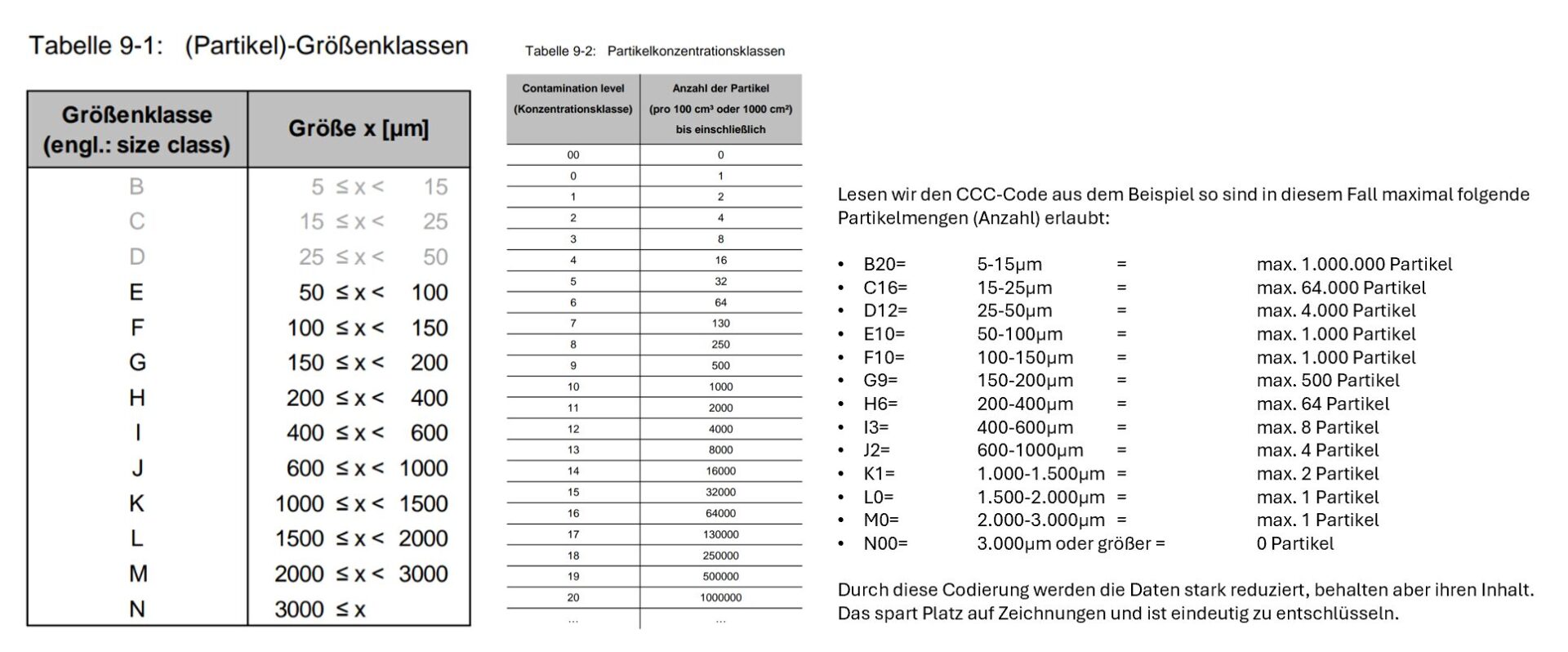
Sauberkeitsanalysen/
Restschmutzanalysen
Extraktionsmöglichkeiten
- Spülen
- Spritzen
- Anlösen
- Ultraschall
- Abblasen
- Durchströmen
Verfügbare Prüfmedien
- Kaltreiniger (Kohlenwasserstoff basiert)
- VE-Wasser
- Luft (aufbereitet und gefiltert)
Partikelauskunft
- metallisch glänzend
- nichtmetallisch glänzend
- Fasern
Mögliche zu analysierende Bauteildimensionen
- Kleinstbauteile im mm Bereich
- Mittlere Bauteile bis 50 kg
- Große Bauteile bis zu 350 kg und max. 2 m Länge
Analysemethoden
MIKROSKOPIE
Automatisierte lichtmikroskopische Analyse von partikulären Verunreinigungen auf Bauteilen nach Extraktion auf einer Filtermembran. Klassifizierung von metallisch und nicht metallisch glänzenden Partikeln sowie Fasern gemäß VDA 19.1 / ISO 16232 oder nach individuellen Kundenanforderungen.
REM-EDX
Materialanalyse Ihrer metallischen, mineralischen und abrasiven Partikel . Durch die Materialbestimmung ermitteln wir die potenzielle Leitfähigkeit und Härte der Partikel, um deren Schädigungspotenzial zu bewerten. Zusätzlich ermöglicht die Analyse Rückschlüsse auf die Partikelherkunft, sodass Sie gezielt die Ursache der Kontamination eliminieren können.
FTIR
Organische Partikel werden neben ihrer Größe auf ihr Spektrum hin untersucht. Durch Kenntnis des Spektrums kann deren Schadenspotential ermittelt werden. Außerdem können Sie Rückschlüsse auf die Herkunft des Partikels ziehen und somit die Quelle der Kontamination gezielt eliminieren.
Oberflächenspannung
Bestimmung der Oberflächenspannung mittels Testtinten im Bereich 32 – 44 mN/m in Anlehnung an DIN 53364 bzw. ISO 8296. Die ermittelte Oberflächenqualität gibt Auskunft darüber, ob die Oberfläche sich für nachfolgende Prozesse, wie zum Beispiel kleben oder schweißen eignet. Das ermittelte Ergebnis dient als Maß für den momentanen Zustand auf Ihrem Bauteil.
GRAVIMETRIE
Quantitative Aussage über die Gesamtmasse der extrahierten Partikelfracht = Rückstandsgewicht
mittels 5-stelliger Analysewaage wird die vom Bauteil extrahierte Partikelfracht ermittelt, in dem der Analysefilter vor und nach der Filtration der Analyseflüssigkeit getrocknet und gewogen wird.
Partikelanalyse mittels REM/EDX
Bestimmung des Materials metallischer und mineralischer Partikel
Metallische und mineralische Partikel werden neben ihrer Größe auf ihre Elementzusammensetzung hin untersucht. Durch Kenntnis der Zusammensetzung können die Härte und die Leitfähigkeit der Partikel identifiziert und deren Schadenspotential ermittelt werden. Außerdem können Sie Rückschlüsse auf die Herkunft des Partikels ziehen und somit die Quelle der Kontamination gezielt eliminieren.
Beispiele für harte (abrasive) Partikel:
- Sand, Korunde, Silikate, Oxide und Minerale Keramik
- Materialklassen und Zusammensetzungen von metallischen und mineralischen Partikeln
- Korrelative Materialanalyse einzelner Partikel die den Grenzwert überschritten haben
- Materialanalyse aller Partikel auf der Filtermembran ab 5 µm möglich
- Bestimmung des Schädigungspotenzials von Partikel: Härte, Leitfähigkeit und Magnetismus
VORTEIL: Ermittlung des Schadenspotentials und Informationen zur Herkunft der Partikel
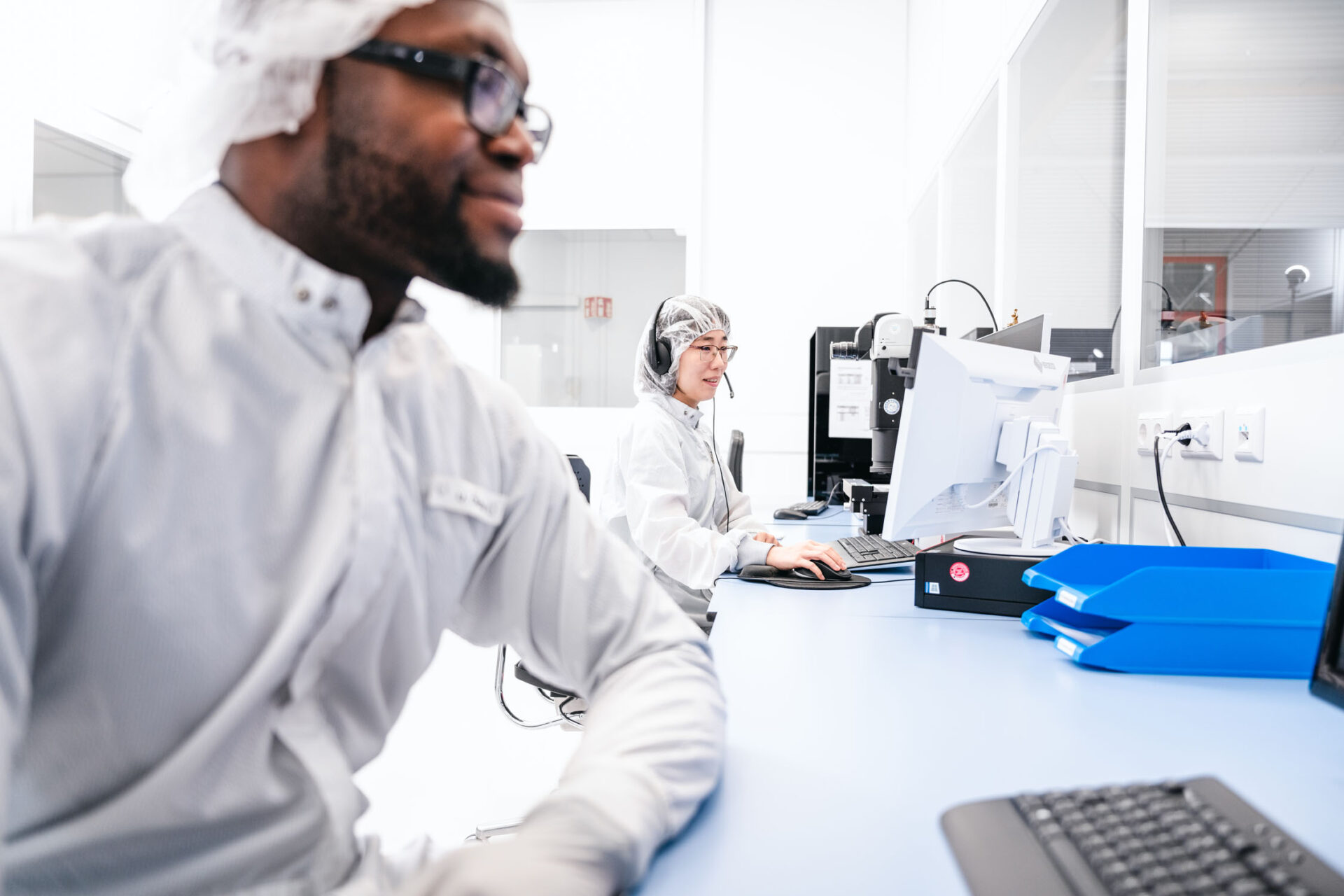
Partikelanalyse mittels FTIR-Analyse
Bestimmung des Materials organischer Partikel (Kunststoff, Holz, Kartonage, etc.)
- Organische Partikel durch Infrarot-Spektroskopie (IR) identifizierbar
- Das gemessene IR-Spektrum wird durch einen Abgleich mit der Datenbank von typischen Materialien identifiziert und das Partikelmaterial bestimmt
- Das gemessene Spektrum kann mit Referenzmaterial abgeglichen werden, Rückschlüsse auf Herkunft von organischen Verunreinigungen sind somit möglich (z.B. Kunststoffe, Verpackungsverunreinigungen, Textilfasern)
- IR-Analyse durch Präparation des Partikels auf ATR-Kristall des FTIR-Mikroskops
- Das Ergebnis beinhaltet das Partikelbild, das IR-Spektrum mit Referenz-Spektrum und die Definition des organischen Materials
VORTEIL: Ermittlung des Schadenspotentials und Informationen zur Herkunft der Partikel.
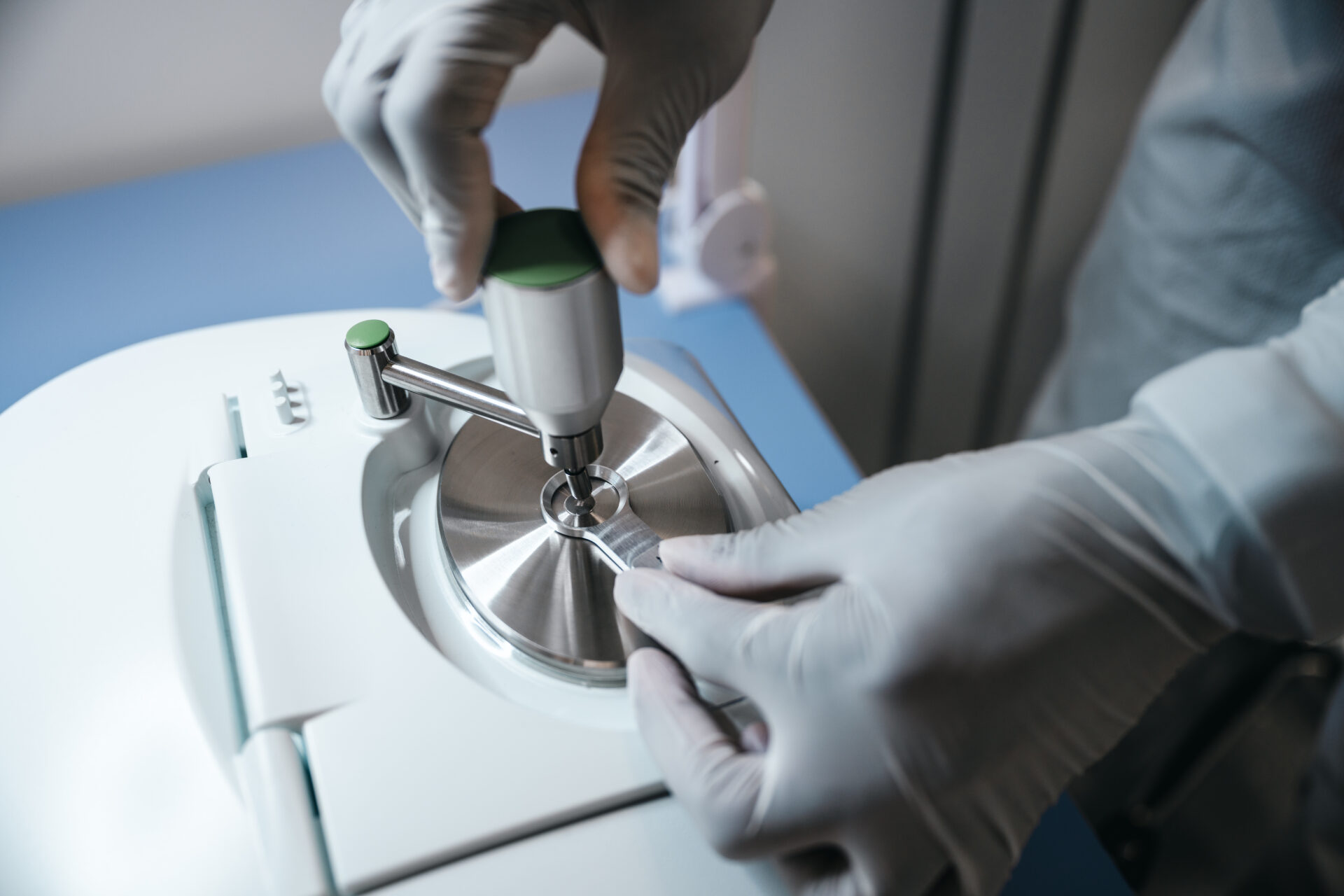
Chemisch-Filmische Analysen
Bestimmung von organischen, ionischen und chemischen Verunreinigungen auf Bauteilen
Neben Partikeln und Fasern sind auch filmische Verunreinigungen wie Rückstände von bspw. Kühl- und Schmierstoffen Quellen für organische Kontaminationen auf Ihrem Bauteil, die schnell zu Störungen in weiteren Herstellungsprozessen führen können. Mittels verschiedenen Analyseverfahren erhalten Sie detaillierte Informationen über die Art der organischen Verunreinigung und können ihrer Quelle gezielt entgegenwirken.
Beispiele hierfür sind:
- Beschichtungen
- Farbreste
- Konservierungsstoffe und Klebstoffe
- Fette (bspw. Kühl- und Schmierstoffe, Fingerabdrücke)
- Organische Partikel und Fasern
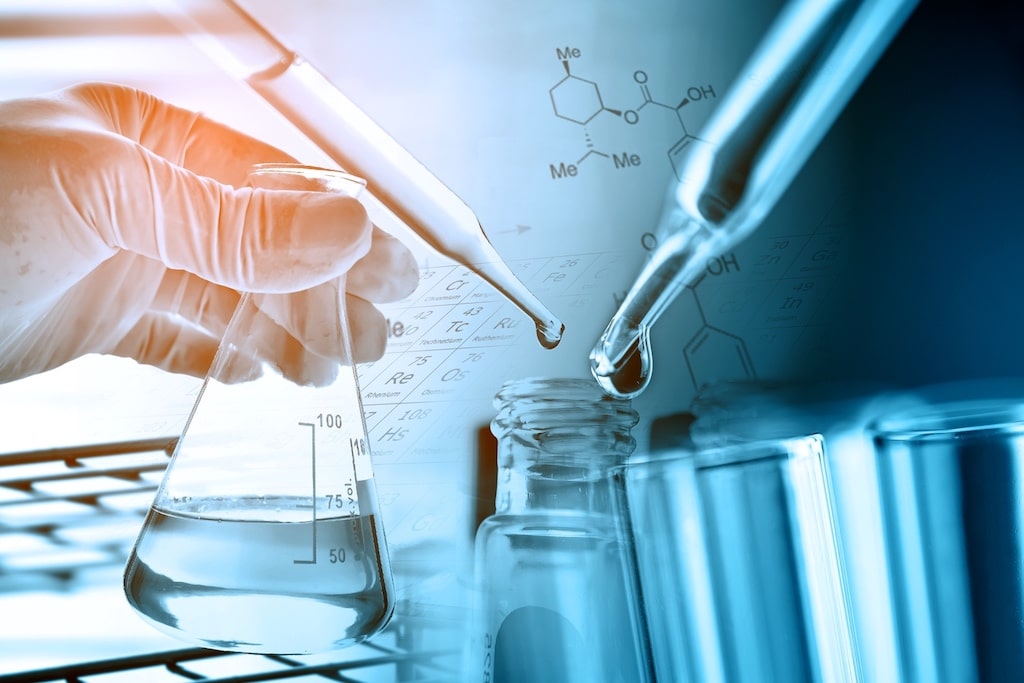
EMISSIONSMESSUNG ¹ ²
Emissionsmessung von Bauteilen mit GC/MS
Für die Ermittlung von flüchtigen Bestandteilen auf Ihren Bauteilen bieten wir eine Analyse im Gaschromatographen mit Massenspektrometer an. Es können kleine Bauteilgrößen (45 mm x 30 mm), über mittlere (245 mm x 265 mm) bis zu großen Größen (555 mm x 870 mm) analysiert werden. Zusätzlich besteht die Möglichkeit je nach Einsatzumgebung Ihres Bauteils die Analyse auch bei höheren Temperaturen bis zu 300 °C durchzuführen. Die Messung erfolgt dabei nach VDI 2083 Blatt 17 und in Anlehnung an ISO 12219-3.
IONEN-CHROMATOGRAPHIE ¹ ²
Analyse ionischer Kontaminationen auf Bauteiloberflächen
Falls Sie für die Feststellung der Oberflächenqualität quantitative sowie qualitative Informationen über die Verunreinigung Ihrer Baugruppen benötigen, ist die Analyse mittels Ionenchromatographie (IC) das Richtige. Nach der Extraktion der Verunreinigungen mit Reinstwasser (nach SEMI F57 / IPC-TM-650 23.28.2) erfolgt die Untersuchung des Reinstwassers auf Kationen (nach ISO 14911) oder Anionen (nach ISO 10304-1).
ROSE-TEST ¹ ²
ROSE-Test (ionische Kontaminationsmessung)
Der ROSE-Test erfasst quantitativ die ionische Kontamination auf Ihrer elektronischen Baugruppe, welche als Folge von Löt- und Galvanikprozessen auftreten können. Bei Bauteilen wie Leiterplatten, sind ionische Verunreinigungen häufig Ursache für gravierende Funktionsstörungen. Nach der Extraktion der Oberflächenkontamination erfolgt die Leitfähigkeitsmessung basierend auf IPC-TM-650 2.3.25. Das Ergebnis wird in NaCl-Äquivalenten angegeben. Anhand des Ergebnisses können Sie überprüfen, ob die Vorgaben für die maximal zulässige ionische Verunreinigung erfüllt sind.
GRAVIMETRIE
Gravimetrische NVR-Bestimmung – Test auf nichtflüchtige Rückstände
Basierend auf ISO 759 werden die nicht verdampfbaren Rückstände (NVR) auf Ihrer Bauteiloberfläche mittels Lösungsmittelextraktion separiert und nach dem Verdampfen des Lösungsmittels gravimetrisch analysiert. Diese Analyse dient der quantitativen Bestimmung von nichtflüchtigen Bestandteilen, welche die Qualität und Leistung Ihres Produktes erheblich beeinträchtigen können. Besondere Bedeutung hat dieser Test in der Elektronik- oder Medizingeräteherstellung als auch in der Chemie- und Pharmaindustrie.
TOC MESSUNG ¹ ²
Analyse von TOC
Mit der TOC-Analyse (englisch: total organic carbon) gibt die Summe des gesamten organischen Kohlenstoffs auf der Oberfläche Ihres Bauteils an und ist ein Maß für dessen organische Verunreinigung. Dazu erfolgt zunächst die Extraktion der Rückstände mittels Reinstwasser und anschließend die Analytik des Extrakts. Dieser Test ist vor Allem für die Überprüfung der Reinigungsqualität von Medizinprodukten wichtig.
1 Diese Analysen fallen nicht in den Bereich unserer Akkreditierung
2 Diese Analysen werden in einem externen Partnerlabor durchgeführt
Flüssigkeit/Öl-Analysen
Bestimmung der partikulären Verunreinigungen in Flüssigkeiten oder Ölen nach ISO 4406/ISO 4407 oder kundeneigener Spezifikationen.
Bestimmung der Reinheitsklasse mittels Filtration der Probenflüssigkeit. Die Partikel werden von einer Membran zurückgehalten und anschließend unter dem Mikorskop analysiert. Automatische Partikelzählung nach ISO 4406/ ISO 4407 oder nach kundenspezfischen Anforderungen.
Bei der Mikroskopie werden die metallischen sowie nicht metallischen Partikel inkl. der Fasern erfasst und Bilder der größten Partikel dem Bericht beigefügt.
Ihre Vorteile auf einen Blick:
- Kontrolle des Waschwassers von Reinigungsmaschinen auf partikuläre Verunreinigungen.
- Analyse von Ölen zur Bestimmung der Reinheitsklassen.
- Monitoring unterschiedlichster Prozesshilfsmittel (Flussigkeiten)
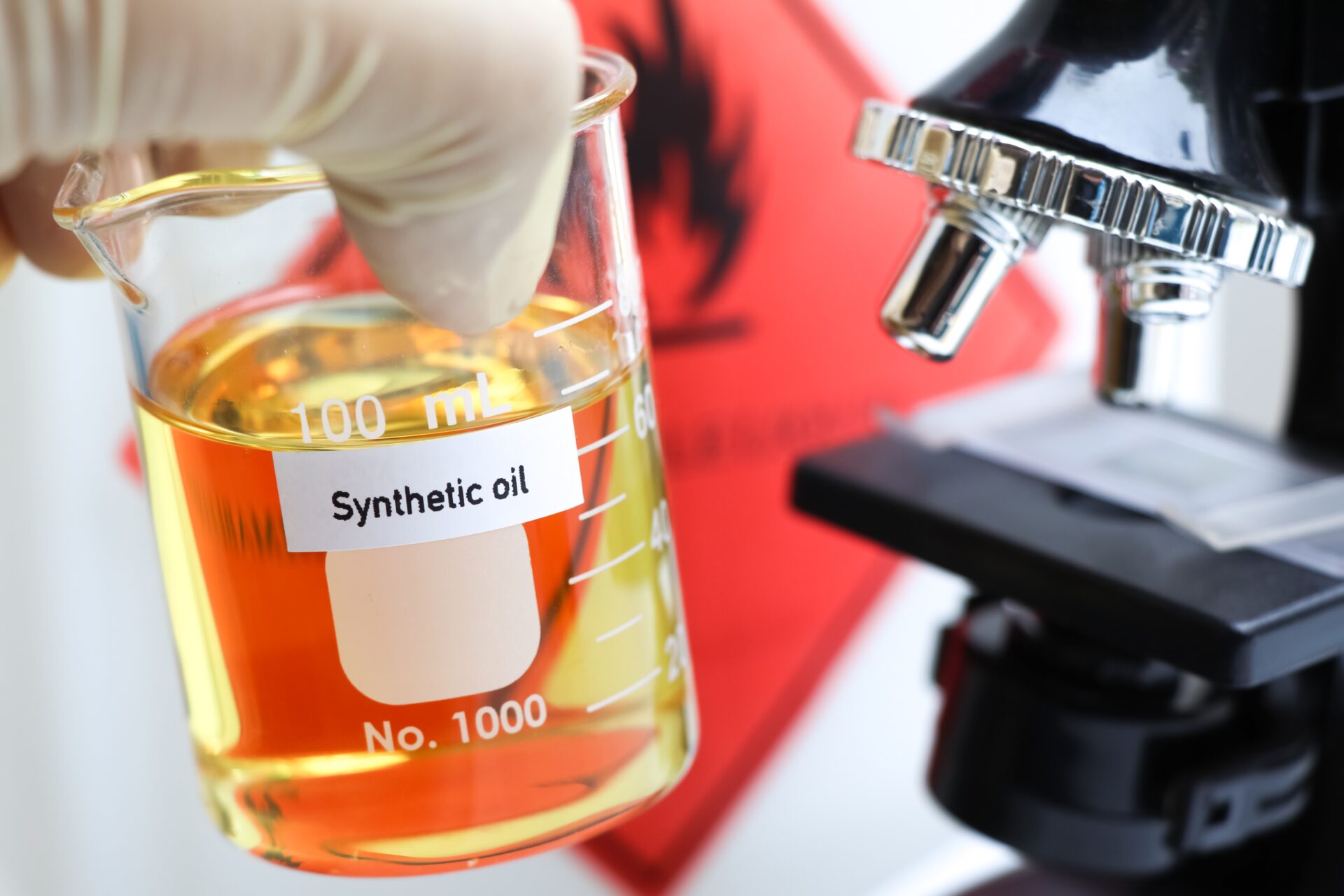
Partikelmonitoring
Die Partikelfalle zur Periodenbetrachtung
Möchten Sie herausfinden, ob sich in Ihrer unmittelbaren Umgebung Ihrer Produktion eine Schmutzquelle verbirgt? Oder wissen Sie bereits, dass Ihre Produktion von Schmutz beeinträchtigt ist, können die Quelle aber nicht herausfinden? Legen Sie einfach über eine bestimmte Zeit eine unserer GLÄSER Partikelfallen aus, um genau dies herauszufinden. Partikelfallen dienen zur Bewertung und Bestimmung von Umgebungsverunreinigungen.
Diese resultieren zum Beispiel aus internen Transportwegen, offenen Eingängen und Fenstern oder auch einem Partikelniederschlag aufgrund von Abrieb. Die Schmutzpartikel legen sich auf dem Klebepad der Partikelfalle nieder und können anschließend einer mikroskopischen Untersuchung zugeführt werden. Schicken Sie die Partikelfalle an unser Labor und wir zählen und messen die Partikel.
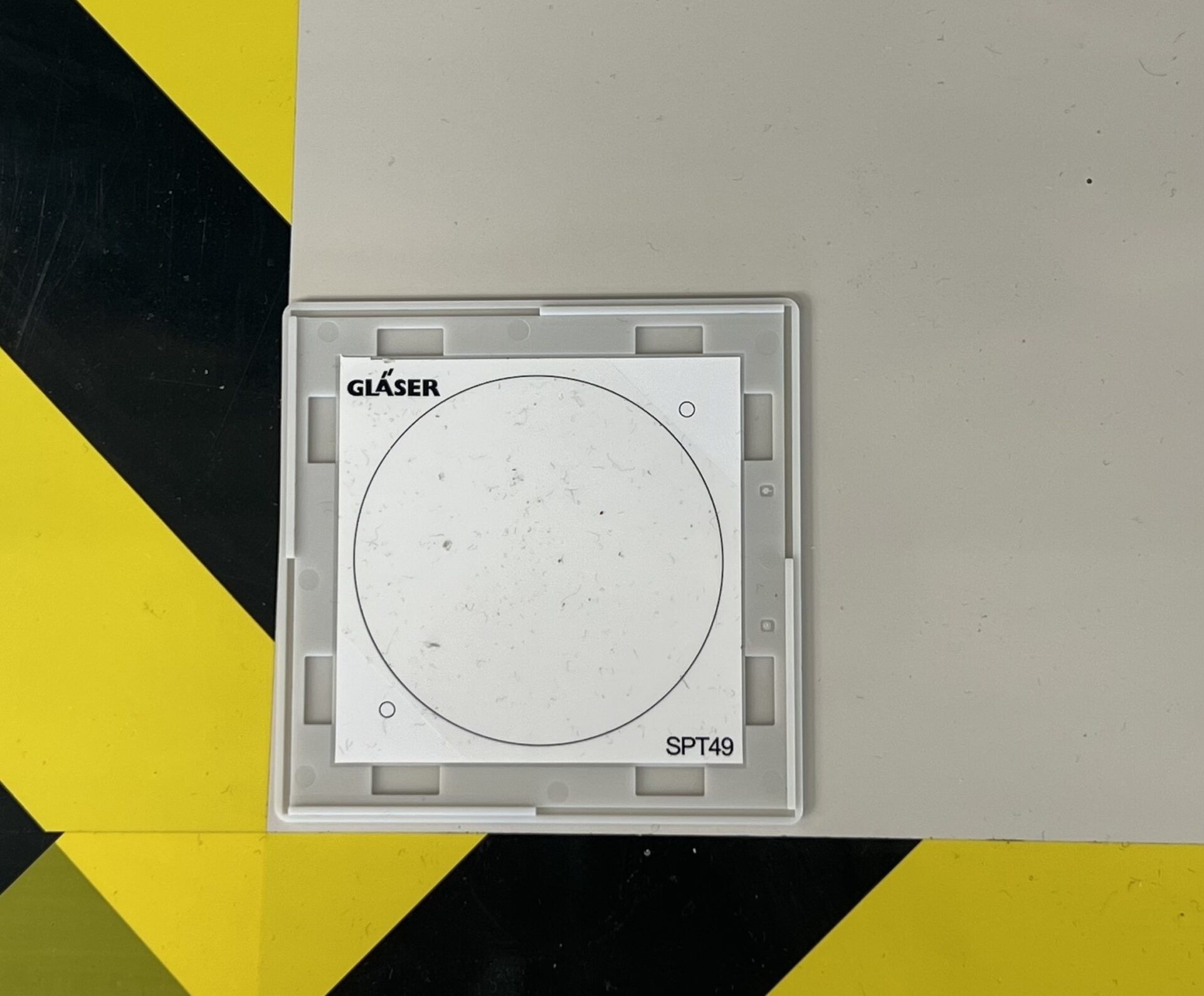
Der Partikelstempel zur Momentaufnahme
Der Partikelstempel dient im Gegensatz zur Partikelfalle zur Bewertung und Bestimmung von Oberflächenverunreinigungen. Mit dem Stempel können Sie einfach Ihre gewünschte Fläche abstempeln und erhalten auf diese Weise eine Momentaufnahme der Verunreinigung an einem bestimmten Ort. Genaue Ergebnisse erhalten Sie durch eine mikroskopische Analyse des Stempels in unserem Labor.
Mit diesen konkreten Ergebnissen können Sie anschließend ganz gezielt Maßnahmen zur Abhilfe der Verschmutzungen einleiten. Ihr Produktionsprozess ist jetzt sauberer!
Das Infoblatt mit weiteren Informationen zur Anwendung der Partikelfalle und des -stempels finden Sie bequem unter Downloads.
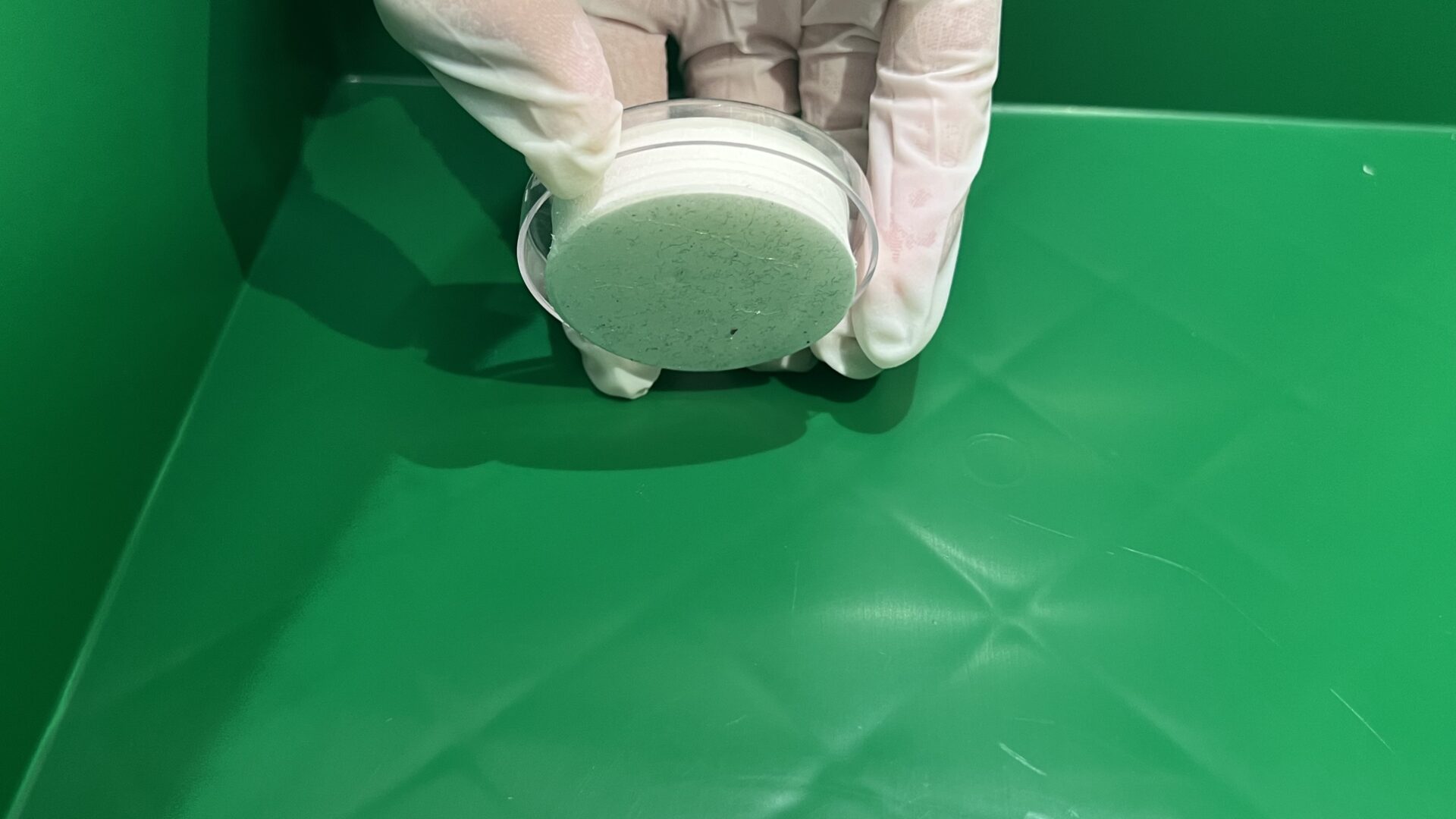
Unser virtuelles Labor
Besuchszeiten: 24/7
Besuchen Sie uns in unserem virtuellen Labor – wann immer Sie möchten. Erkunden Sie unsere Prüfmaschinen, aus eigenem Anlagenbau. Entdecken Sie, was moderne Laborausstattung heutzutage ausmacht. Gläser CleanTec ist im Bereich der Technischen Sauberkeit weltweit führend auf den Gebieten: Maschinenbau, Laboranalytik, Schulung, Consulting, Service und Handel.
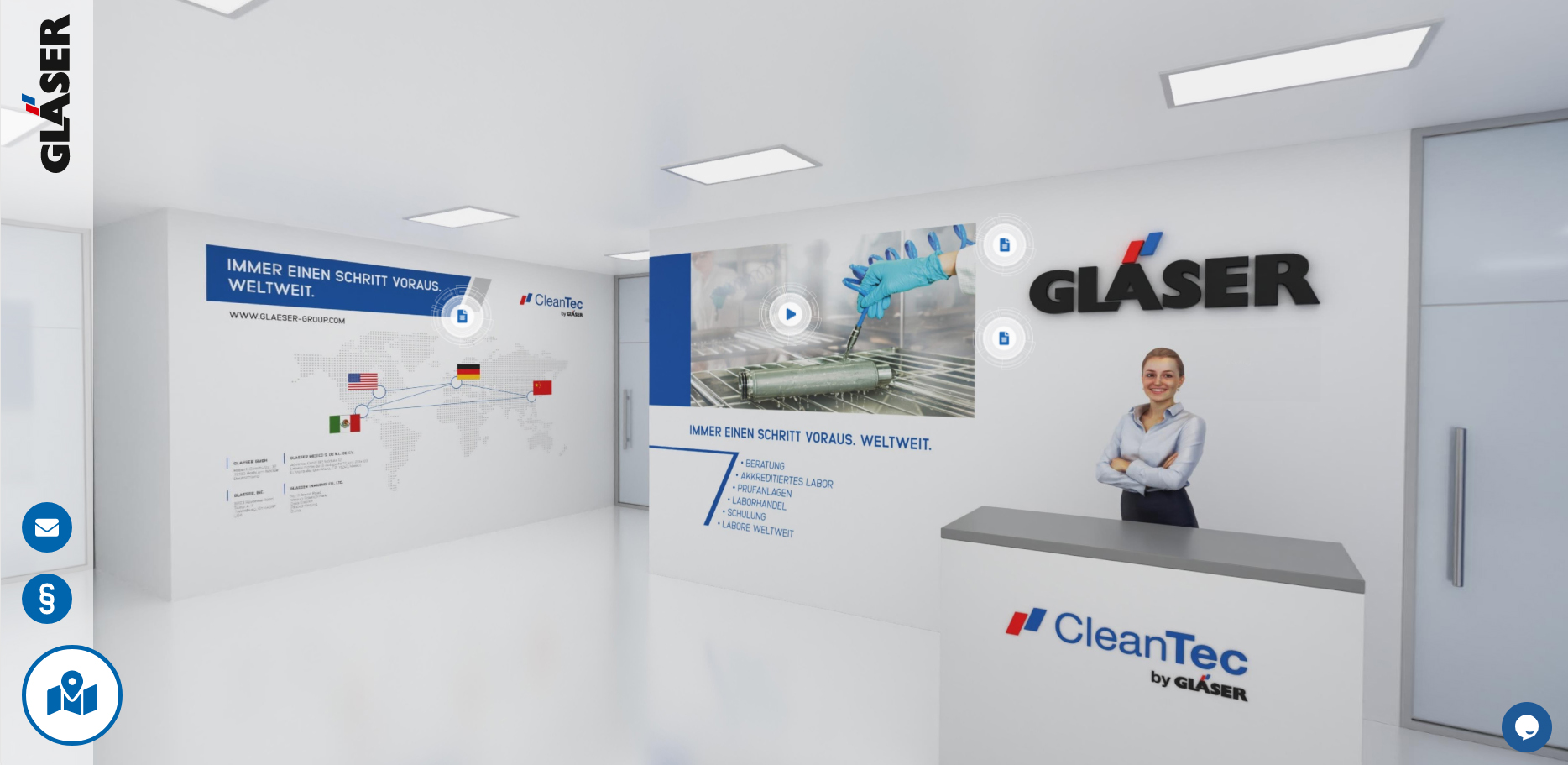